CONSTRUCTION MATERIAL OF THE FUTURE
LEADFRP, a materials technology driven company
LEADFRP has a technological team
Our many years of EXPERIENCE is
the main reason of sucess
Expert team
Production lines
Sales Revenue
Continuous Basalt Fibre (CBF) is a relatively young, but very promising material
Stronger
Cheaper
Environmental
At the present time, just a handful of countries in the world, including the United States and China produce around 15k tons of CBF per year. Market demand by 2025 is calculated to be 200,000 tons per year. Basalt fibre is superior to glass fibre, in terms of thermal stability, heat, sound and electrical insulation, resistance to fire, corrosive chemicals, radiative quality, anti vibration and overall durability while at the same time being environmentally friendly. Continuous Basalt Fibre (CBF) – a product produced by a single step extraction from molten basaltic rock without the use of any chemicals. Basalt Rock is a single-component resource of natural origin; it is an ecologically clean raw material ideal for the production of CBF. World reserves of basaltic rock are endless and cheap, adding less than 5% to the cost of production.
Meet with our expert team
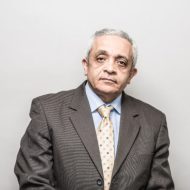
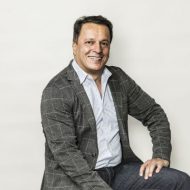
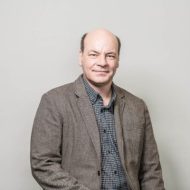
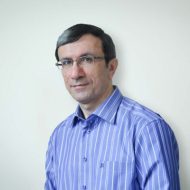
Improve the market competitiveness of partners
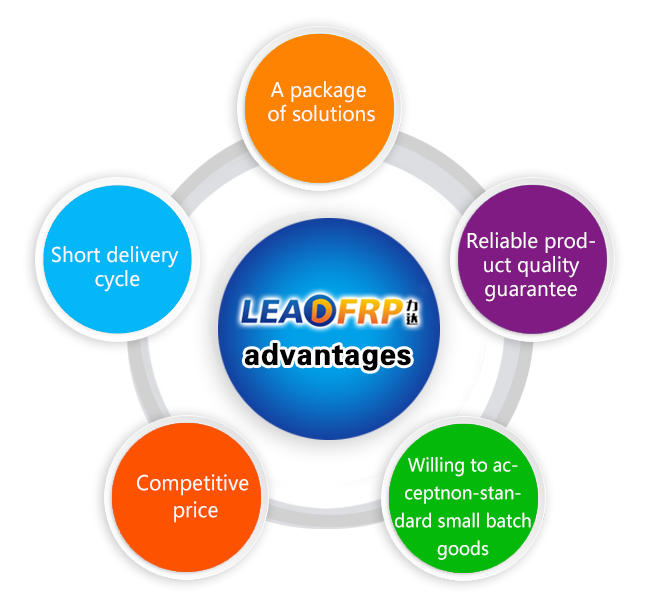
MAINTENANCE FREE
TRANSPARENCY
CORROSION RESISTANT
EASY INSTALLATION
Basalt products used in
construction industry
Our production method allows to compete in cost to steel rebar when taken into account equal strength replacement.
Basalt FRP rebar represents non-metallic reinforcement rods of various actual lengths and outer diameter with dimensions from 4 to 32 mm. Basalt FRP rebar is produced by the method of pultrusion and epoxy resin. Due to unique performance properties, it is an efficient and cost effective alternative to steel reinforcement.
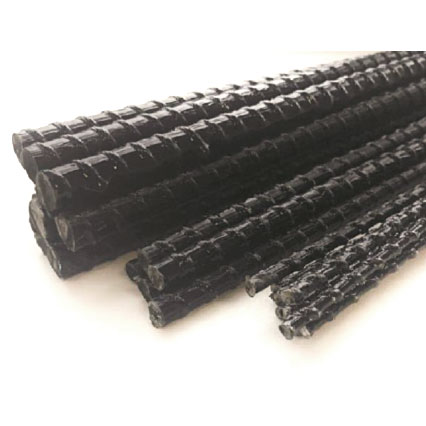
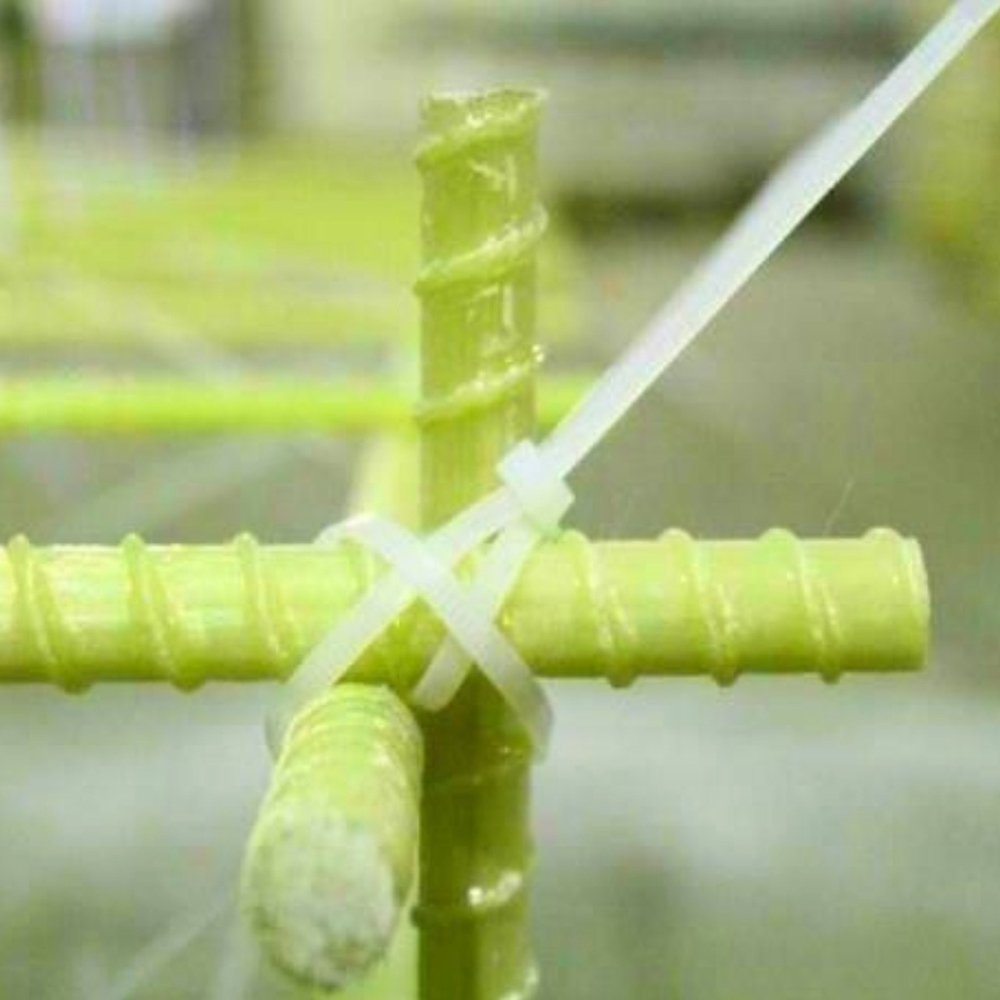
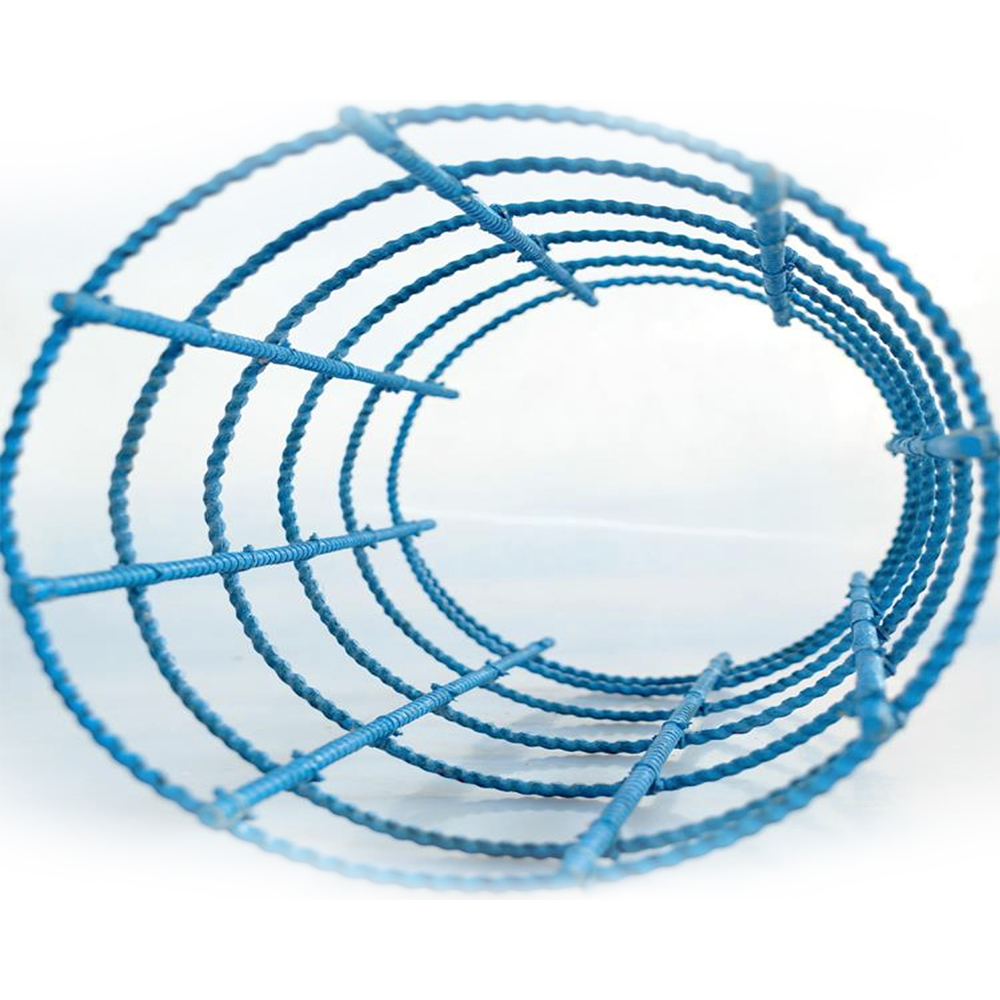
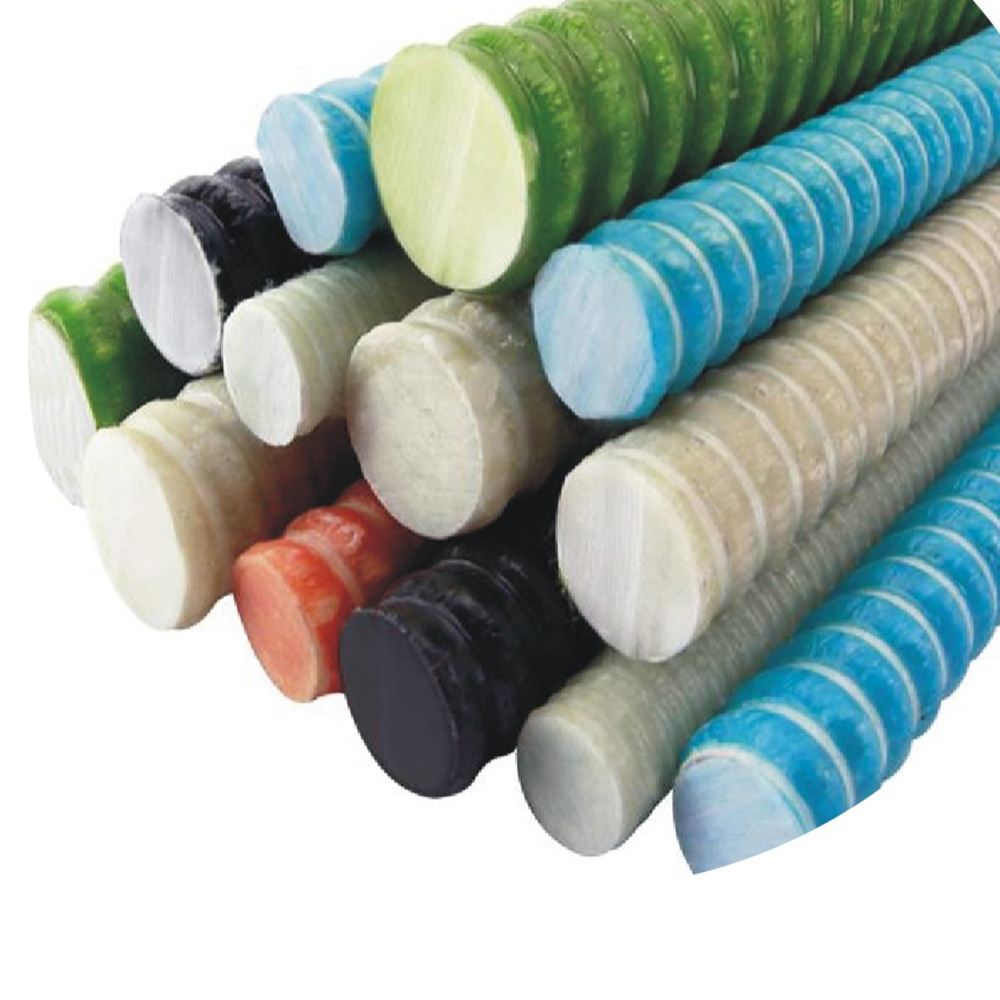
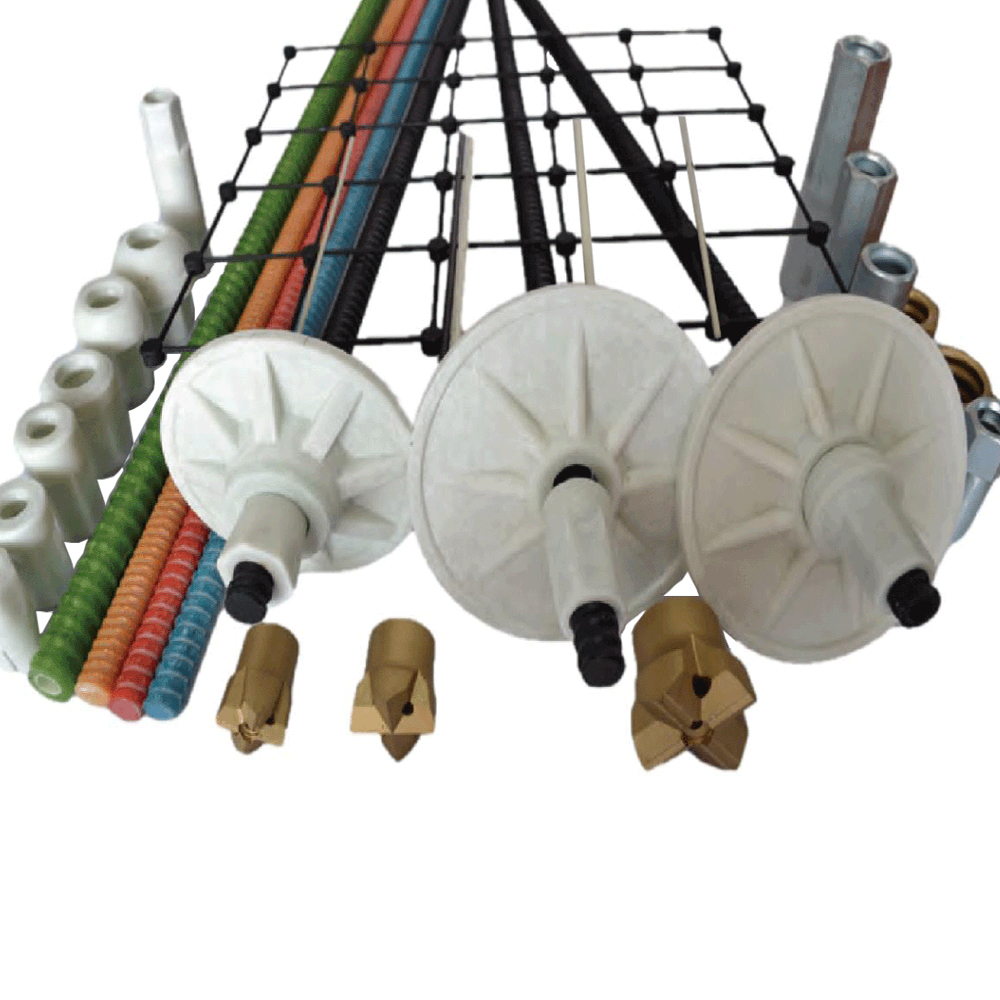
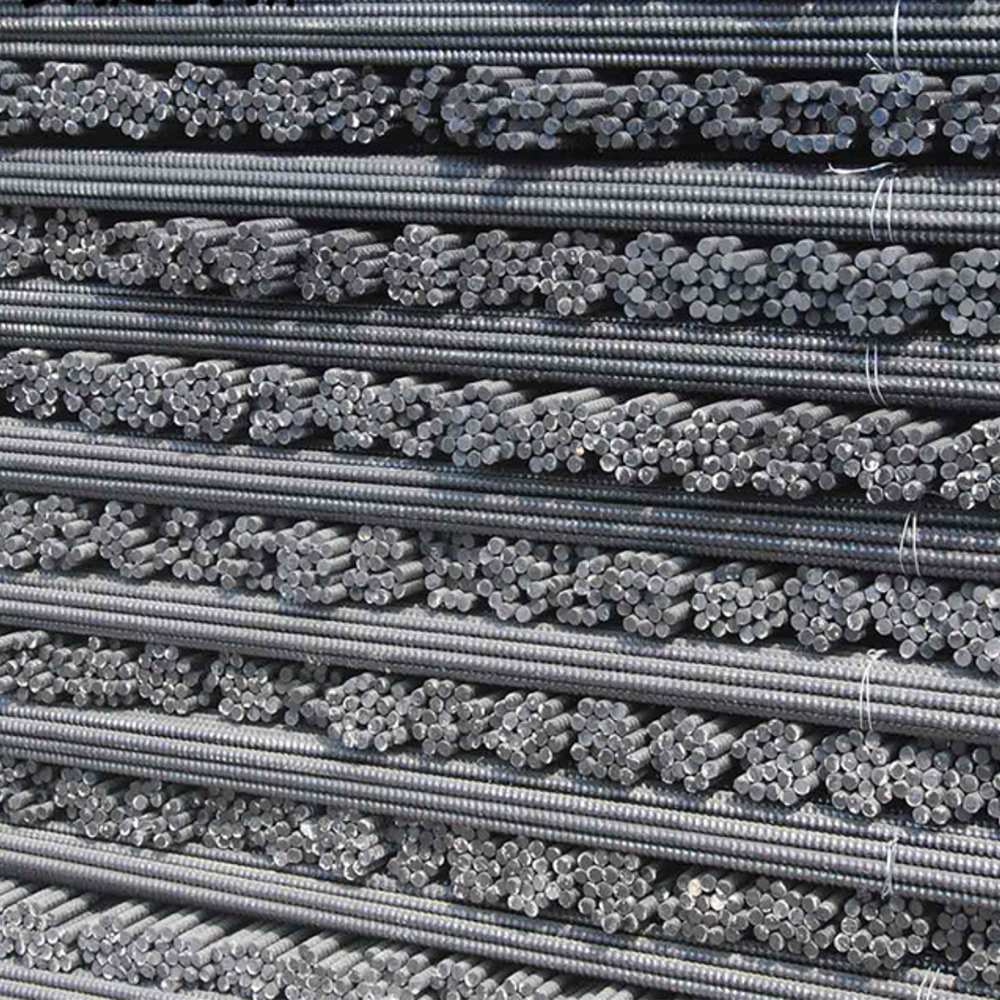
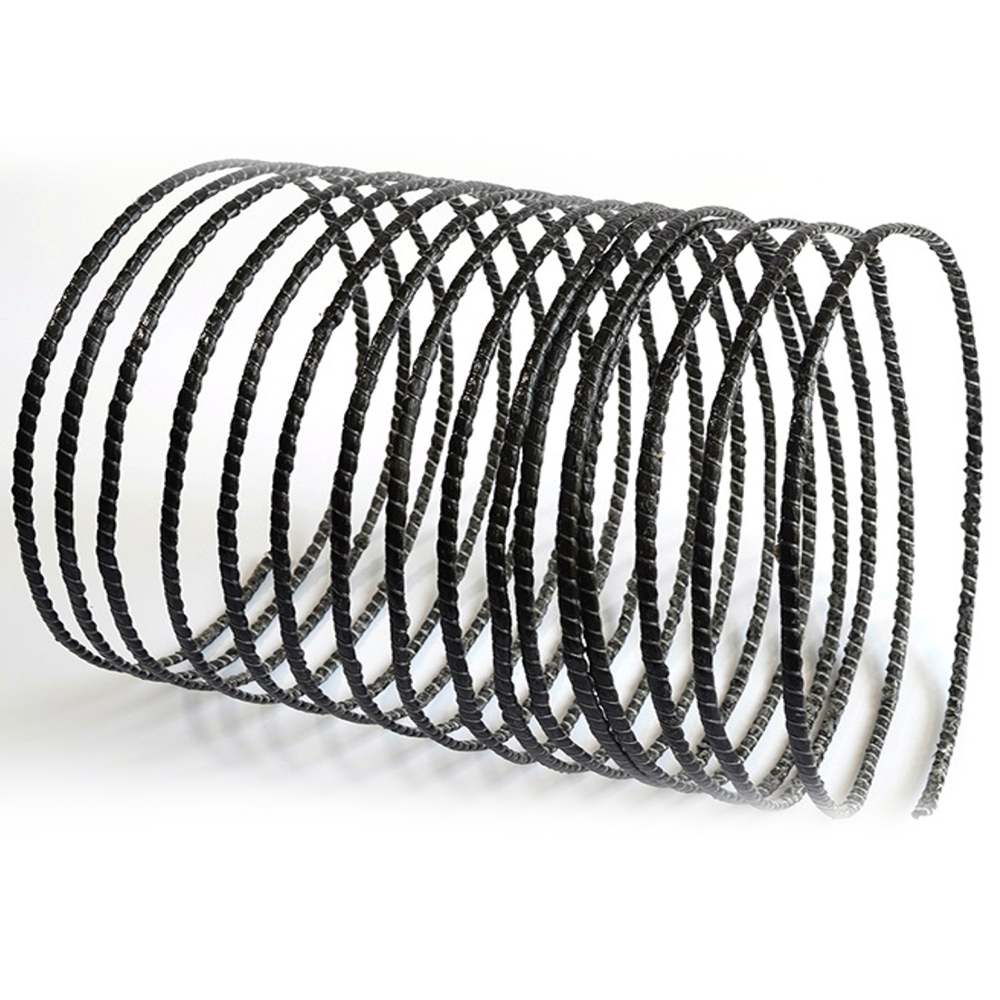
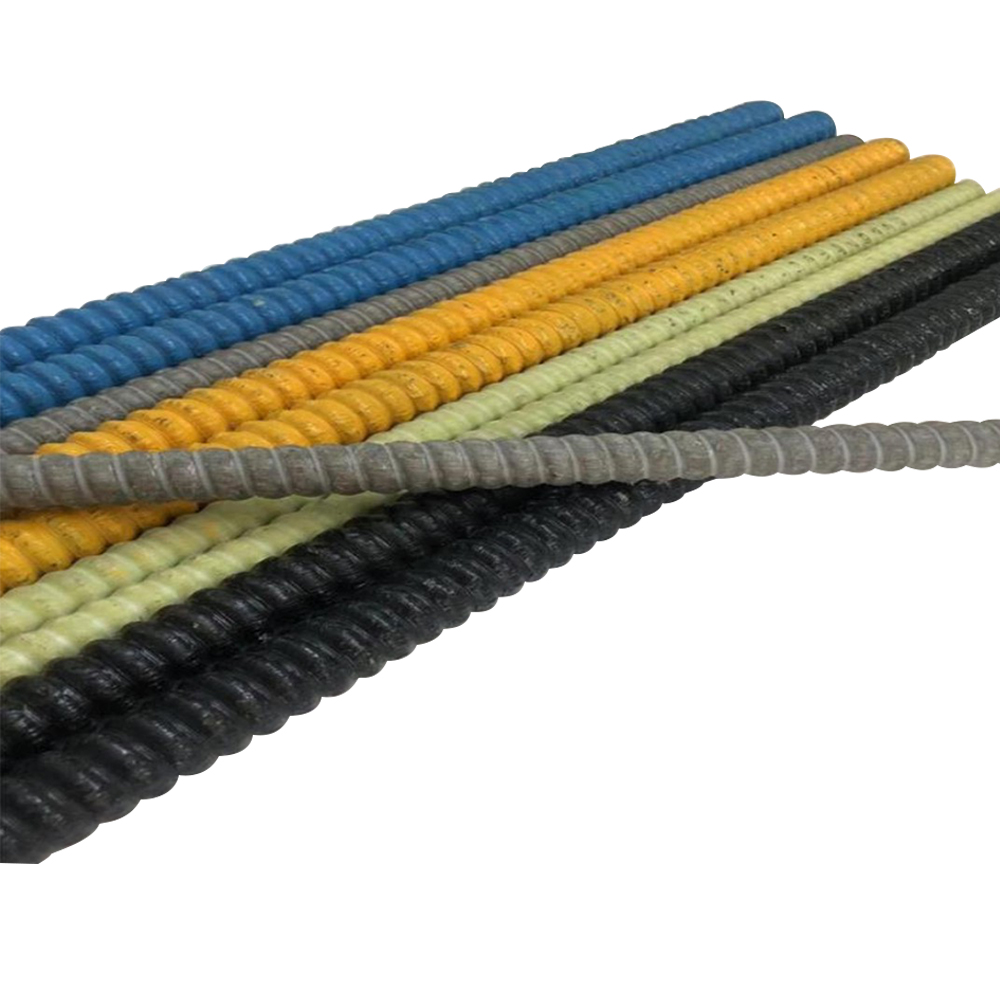
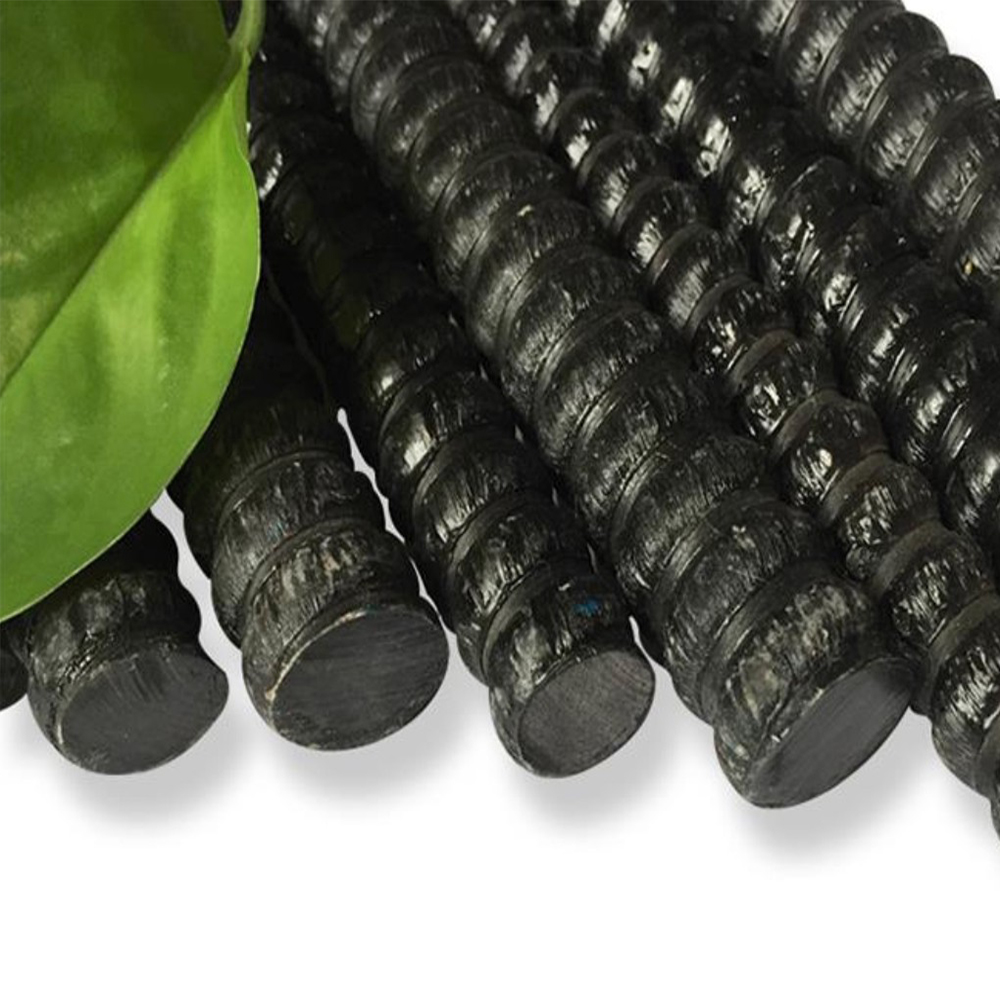
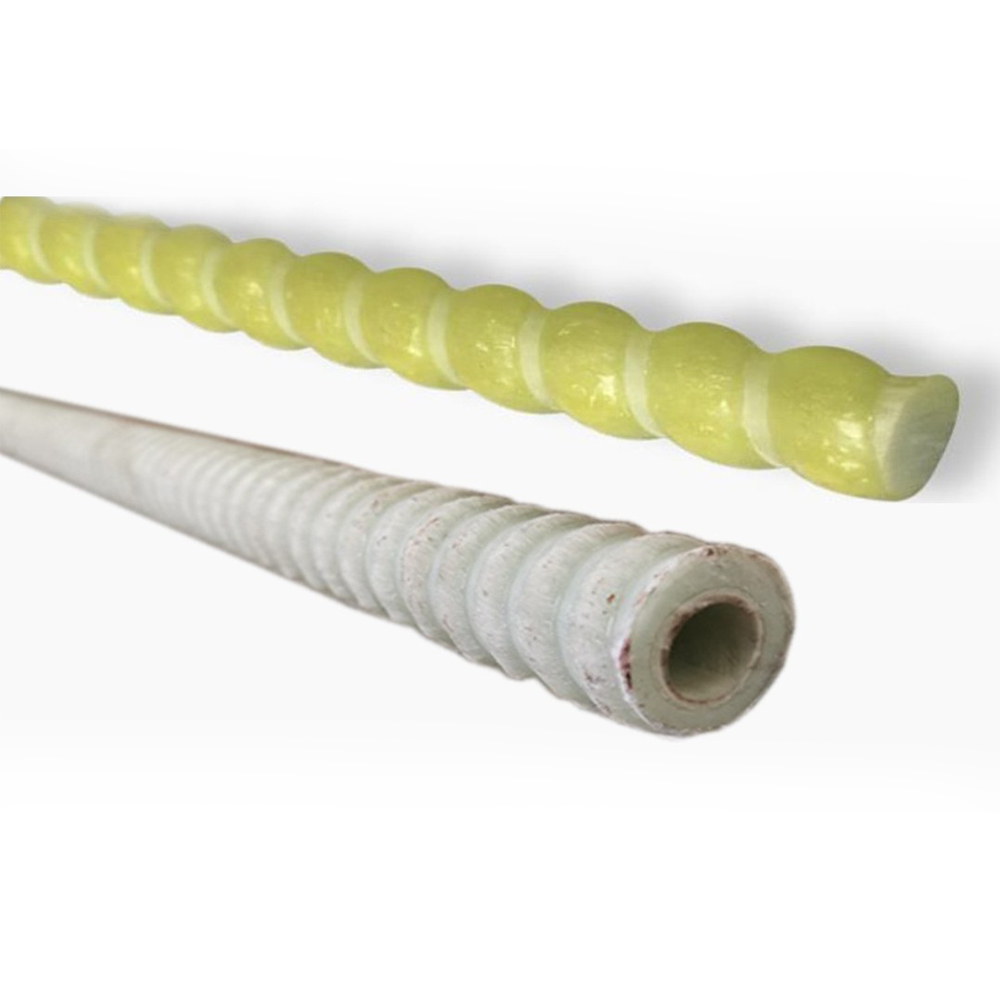
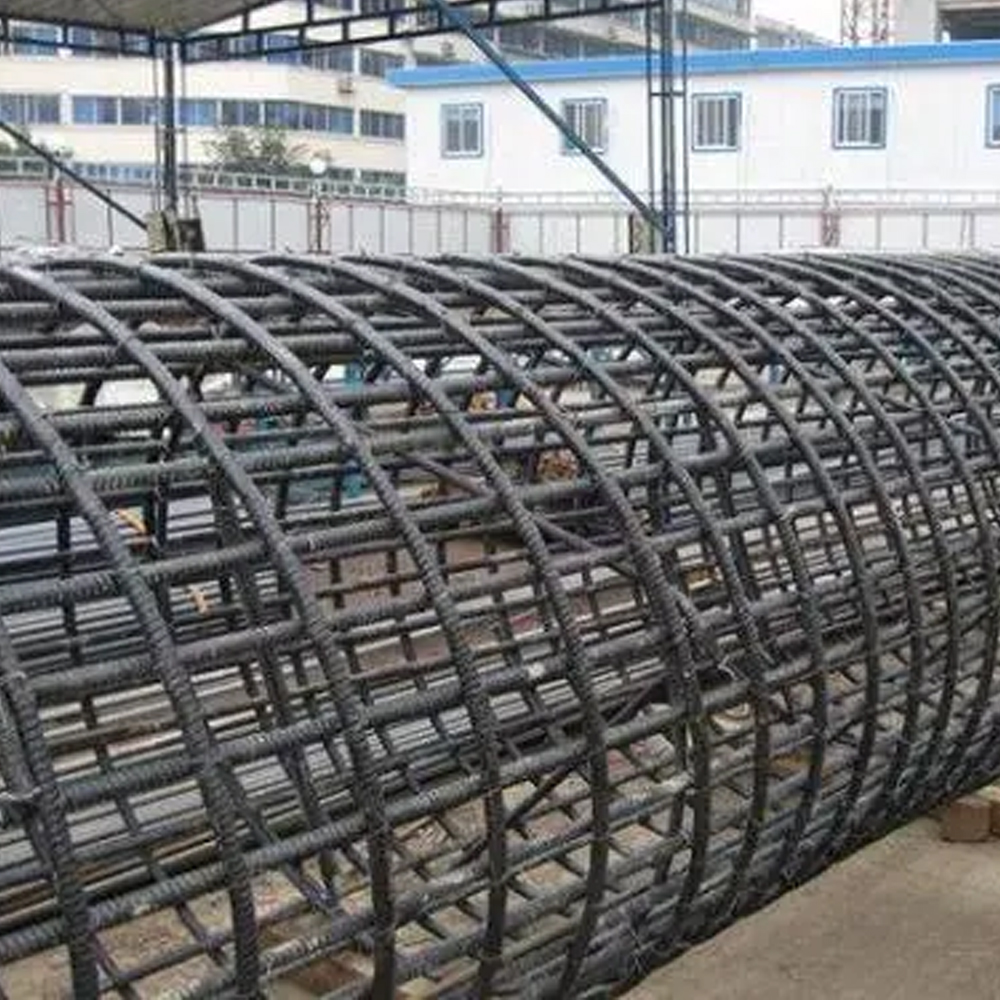
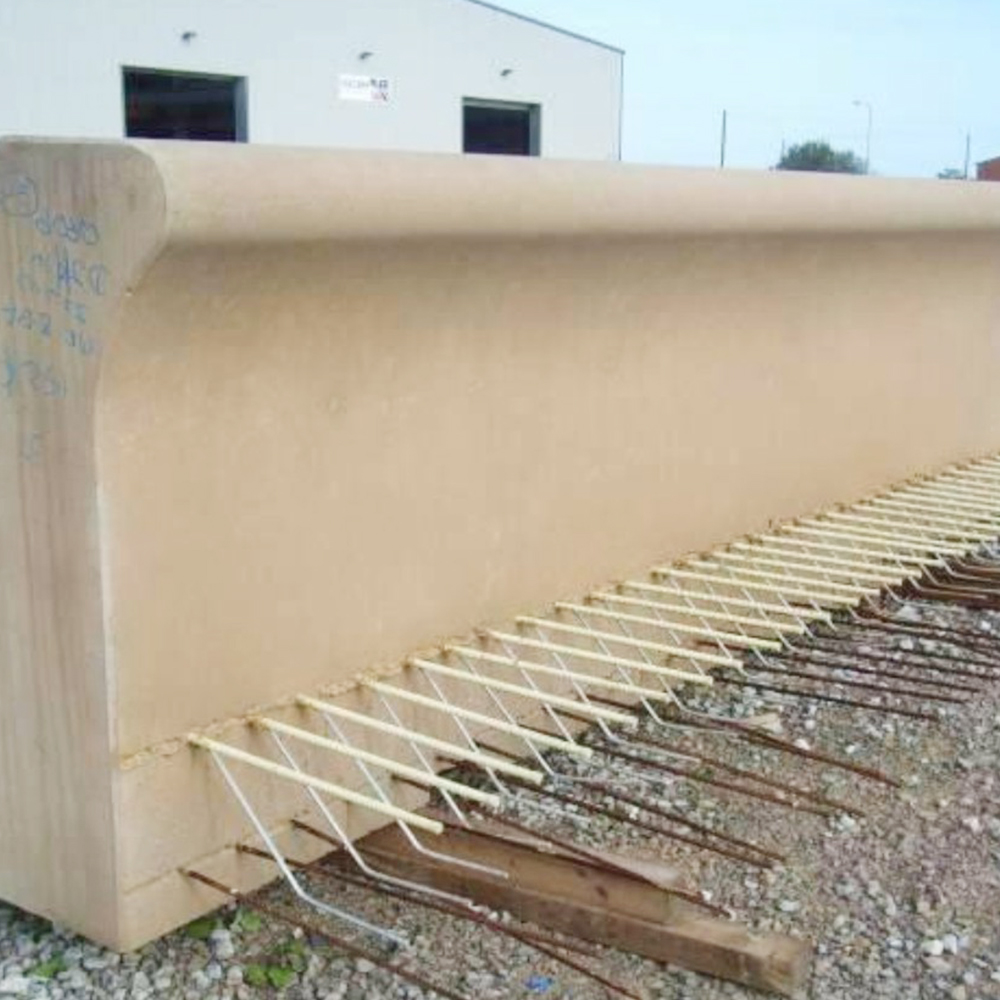
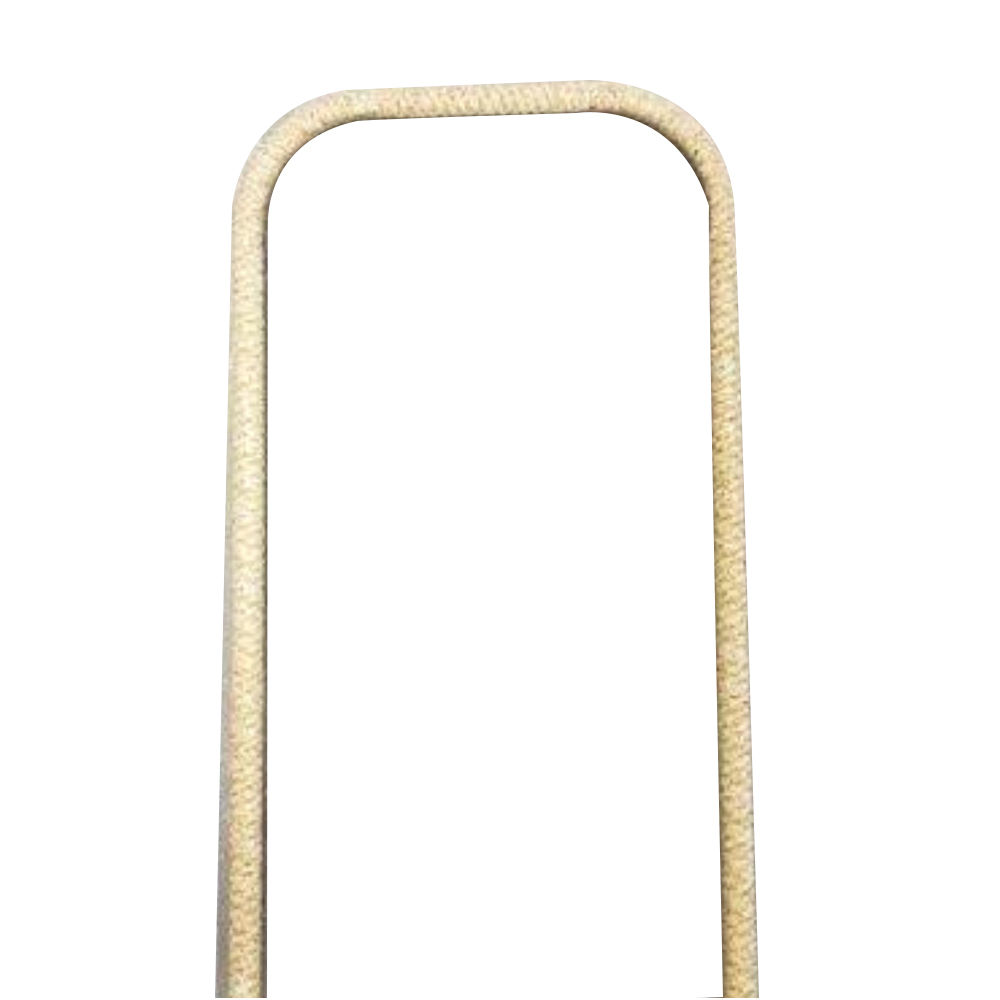
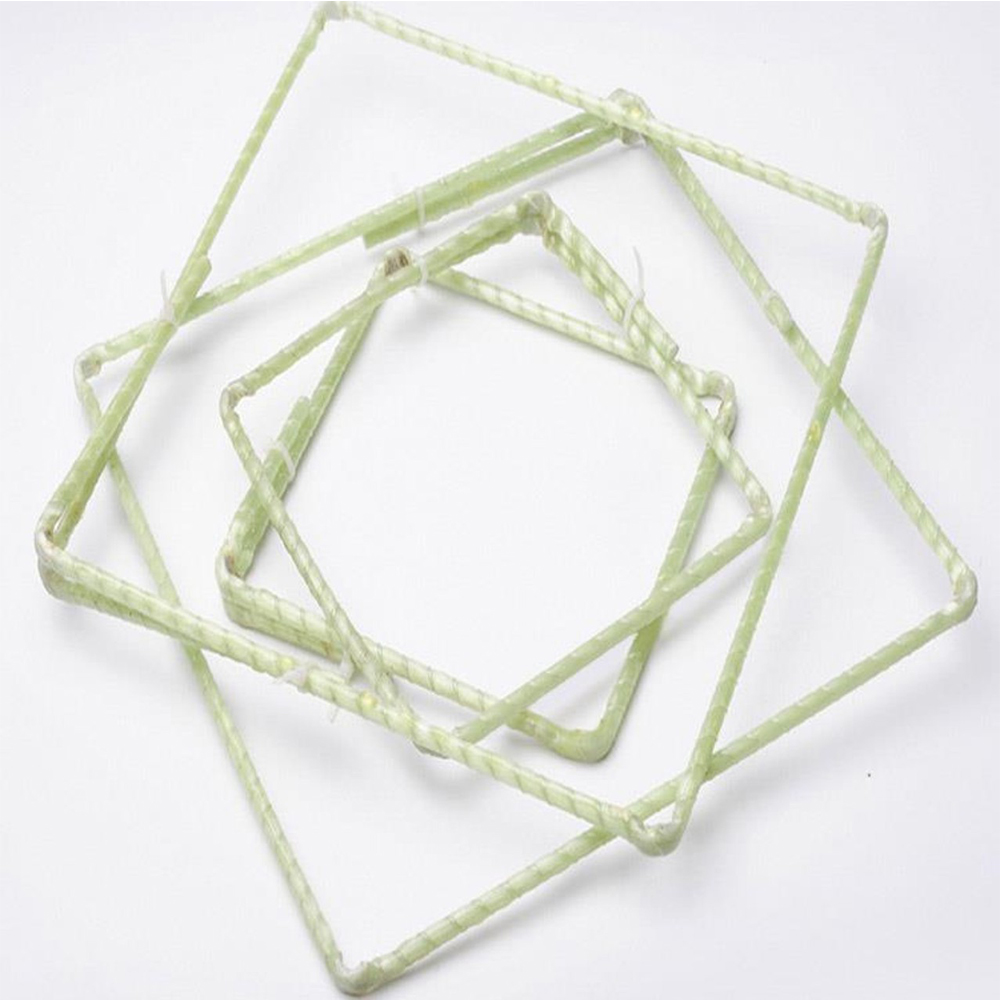
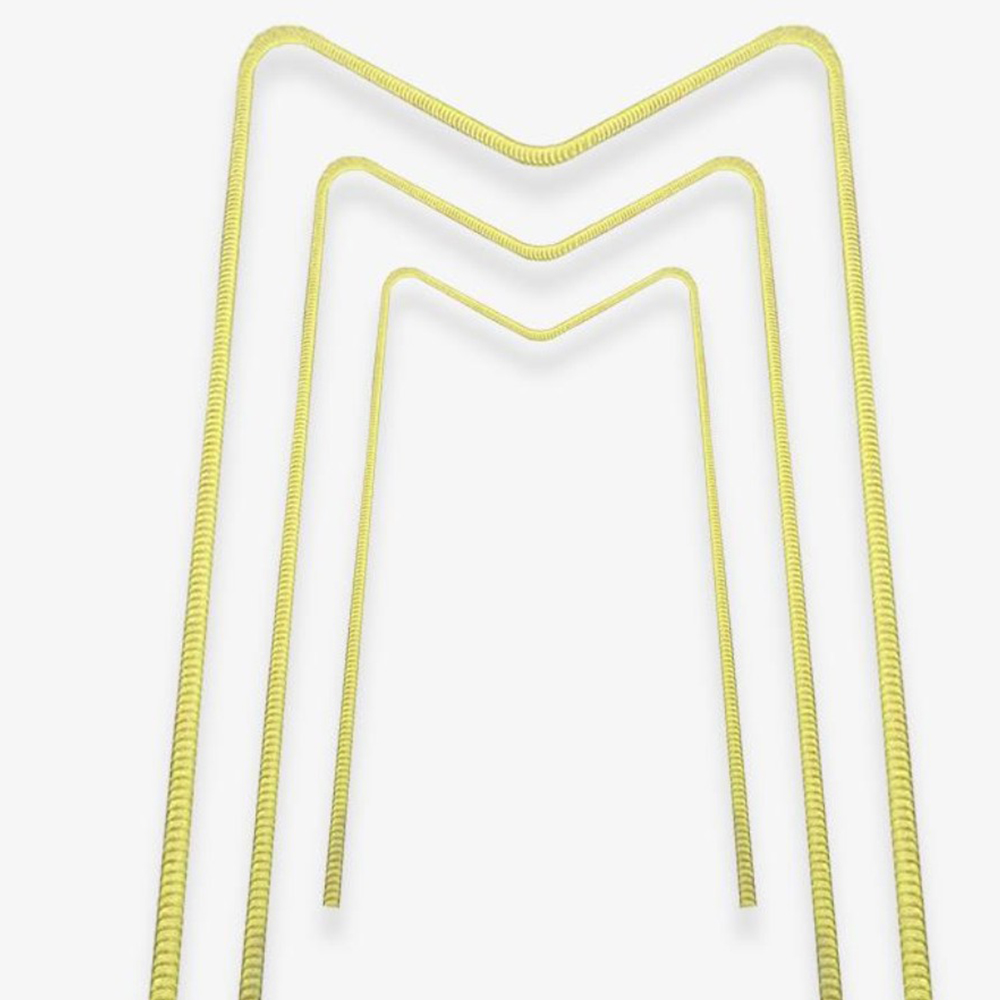
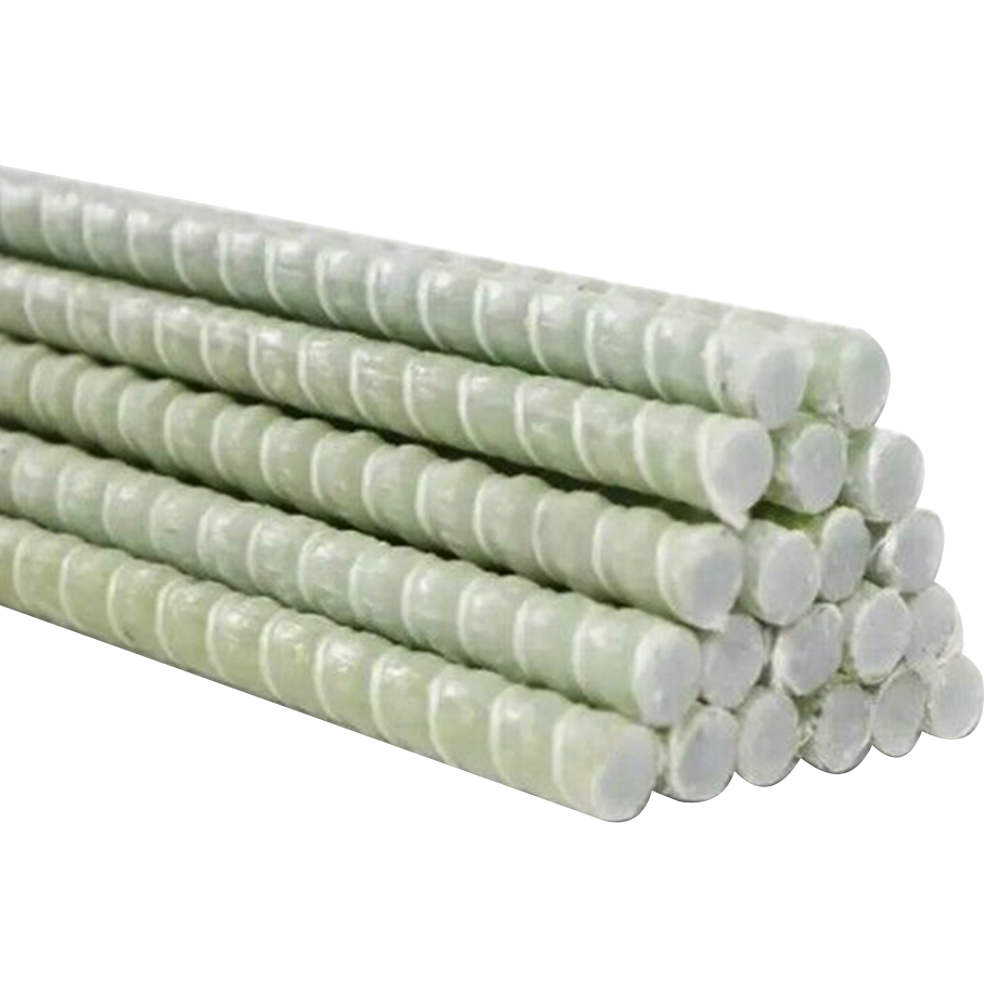
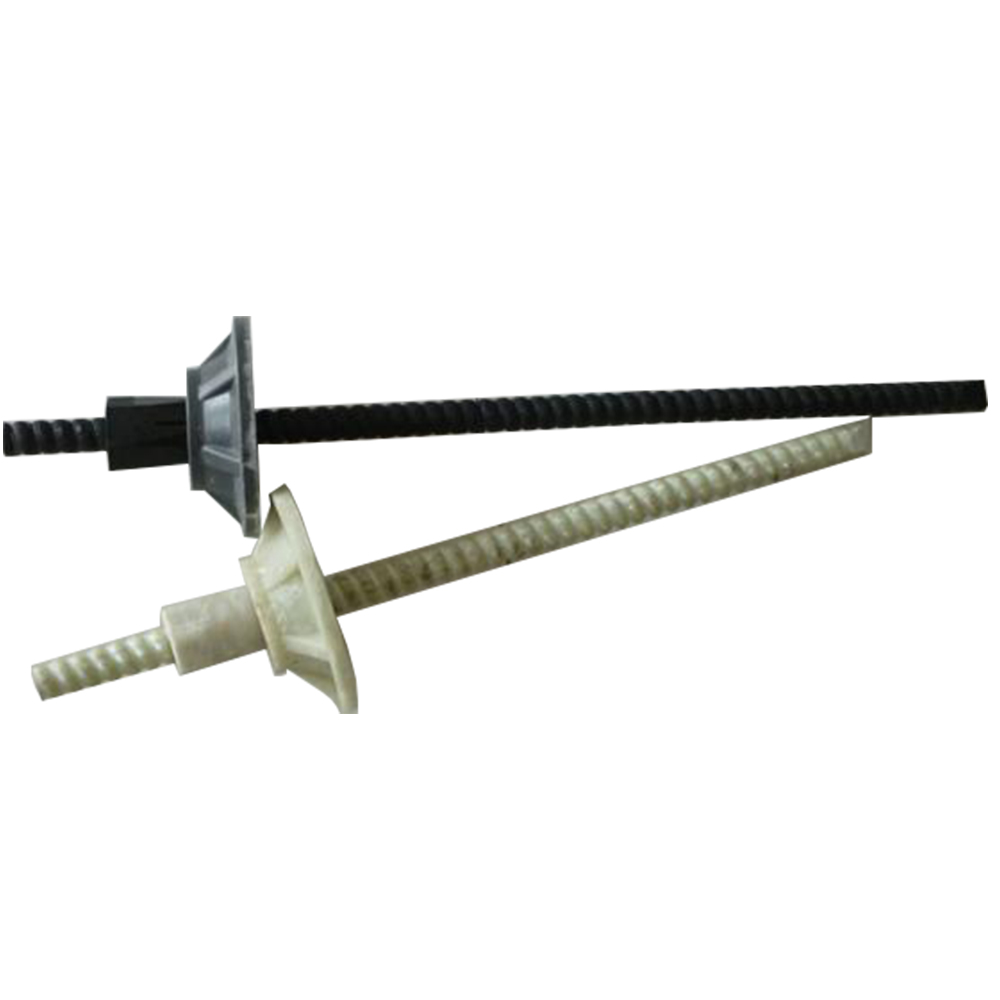
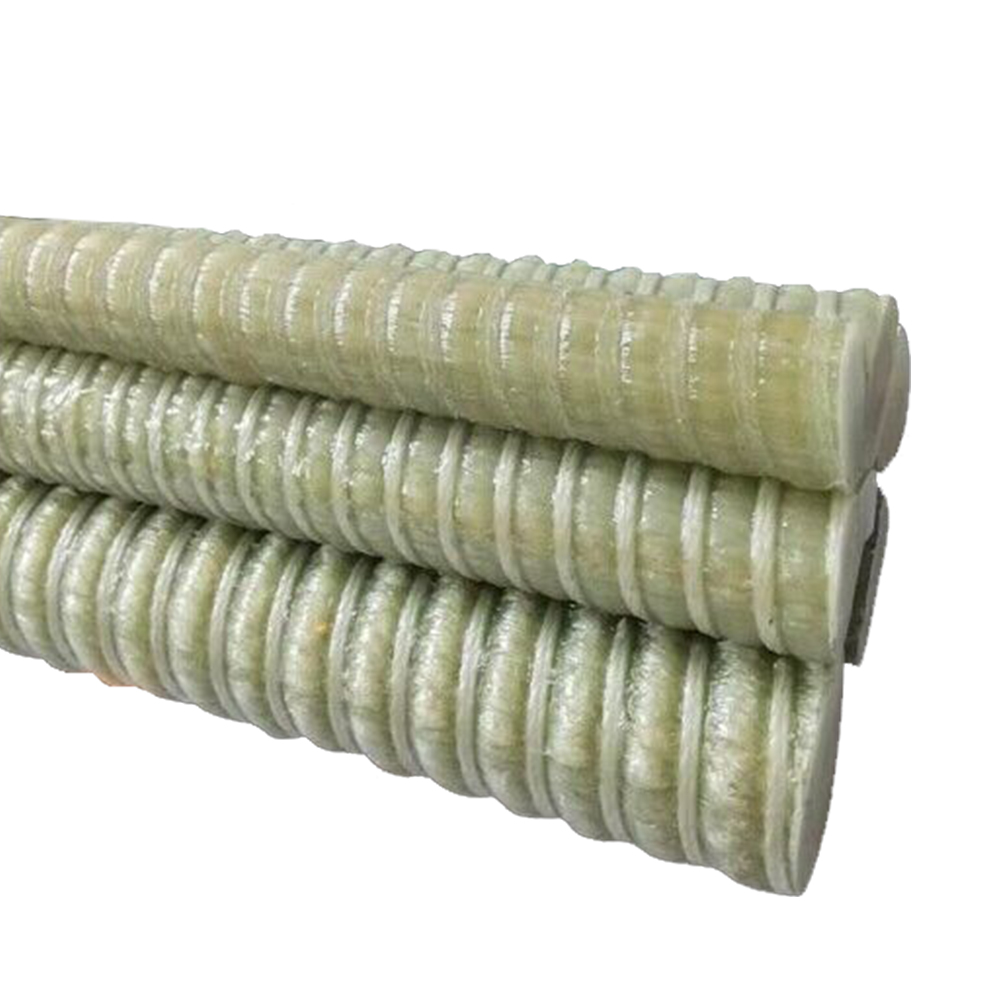
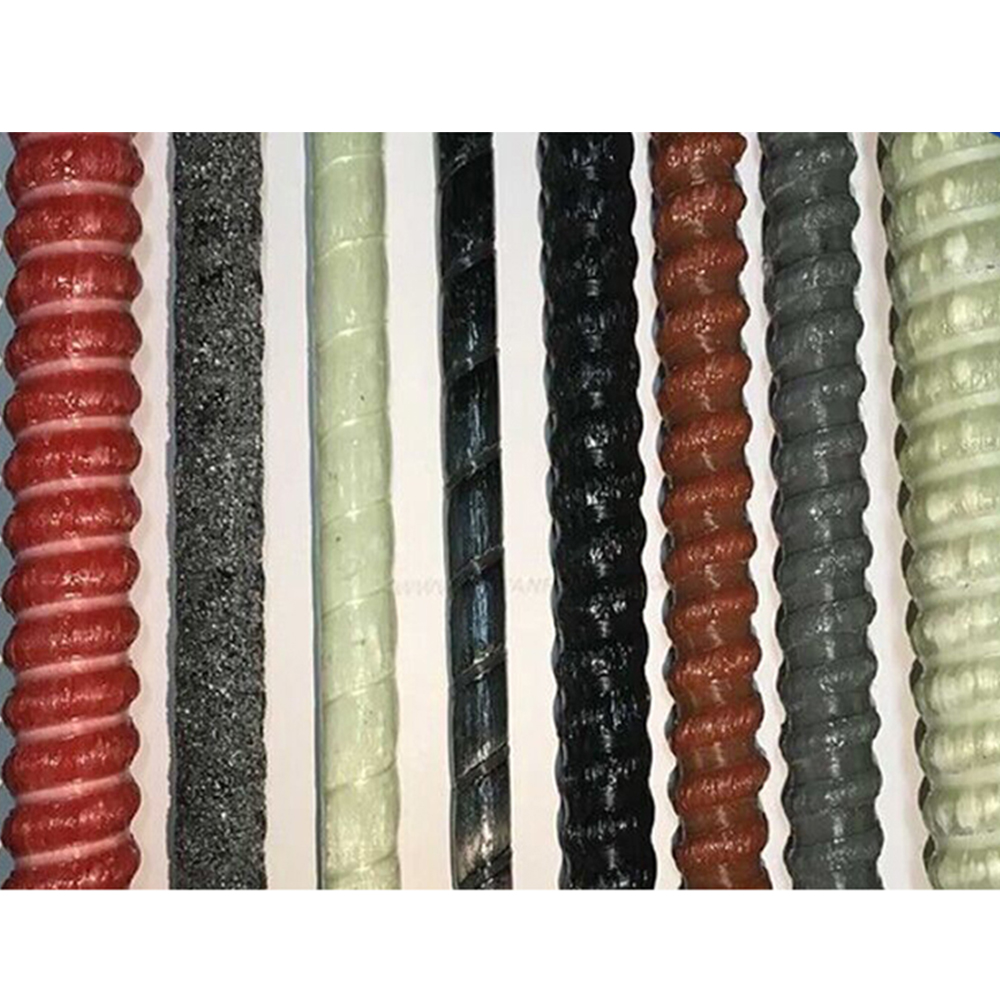
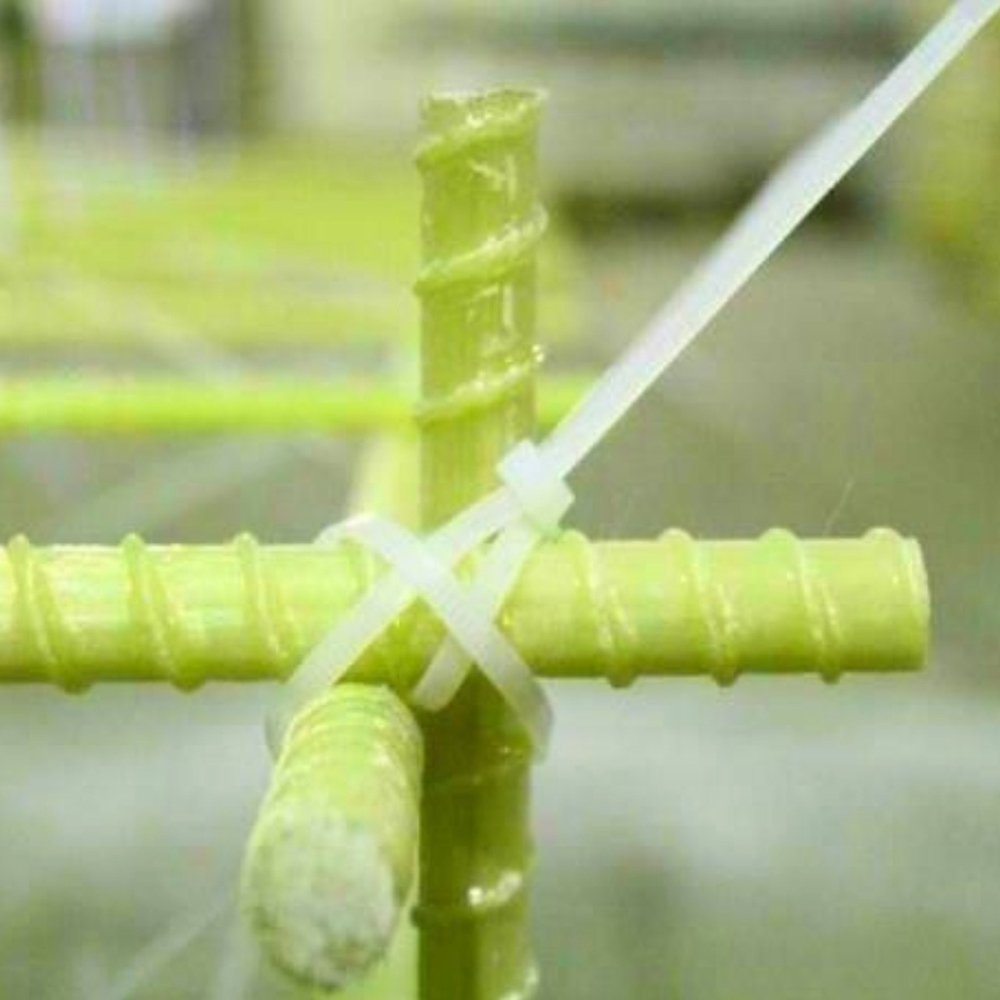
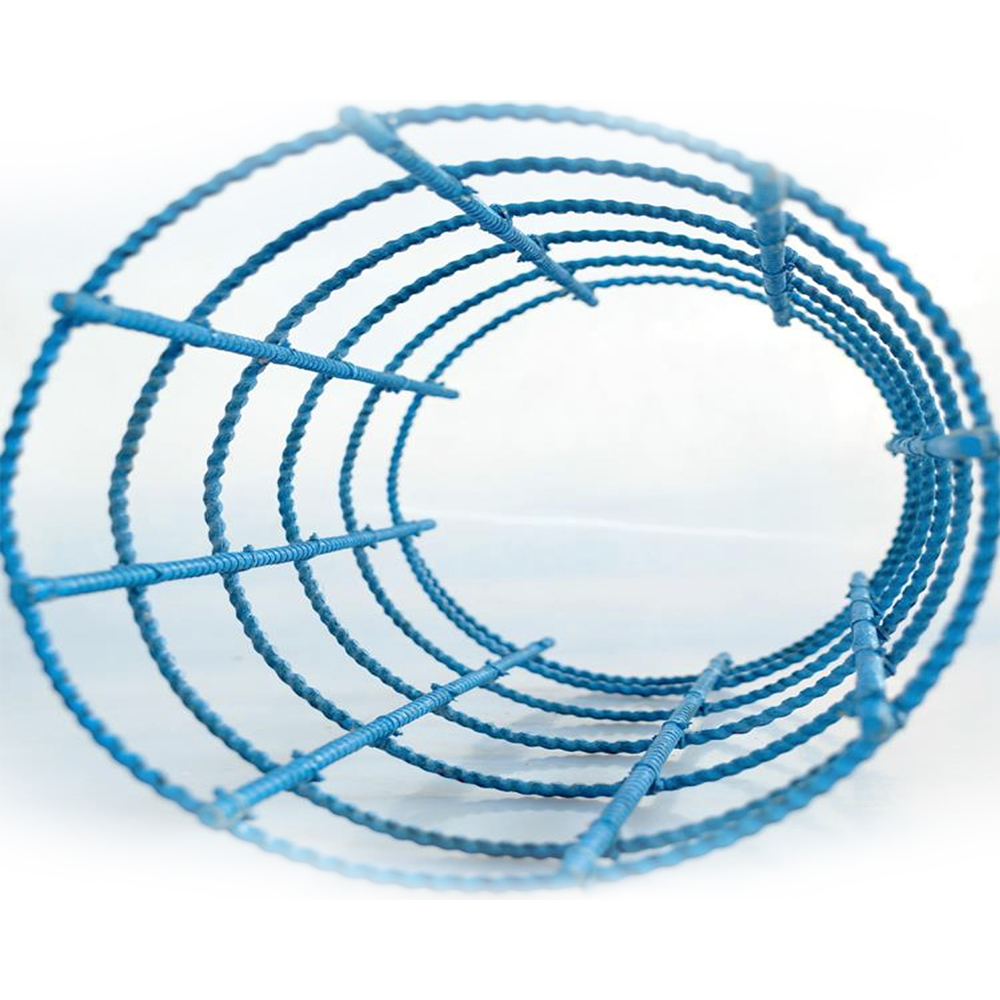
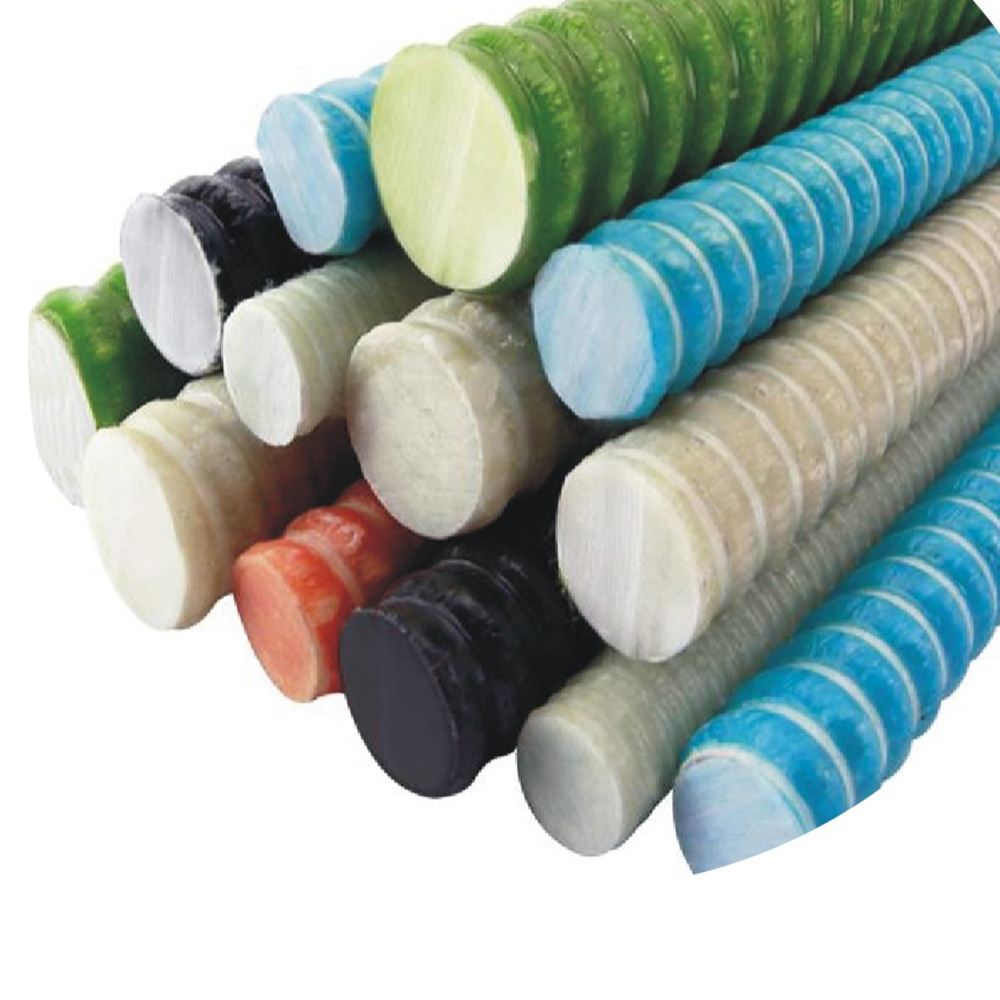
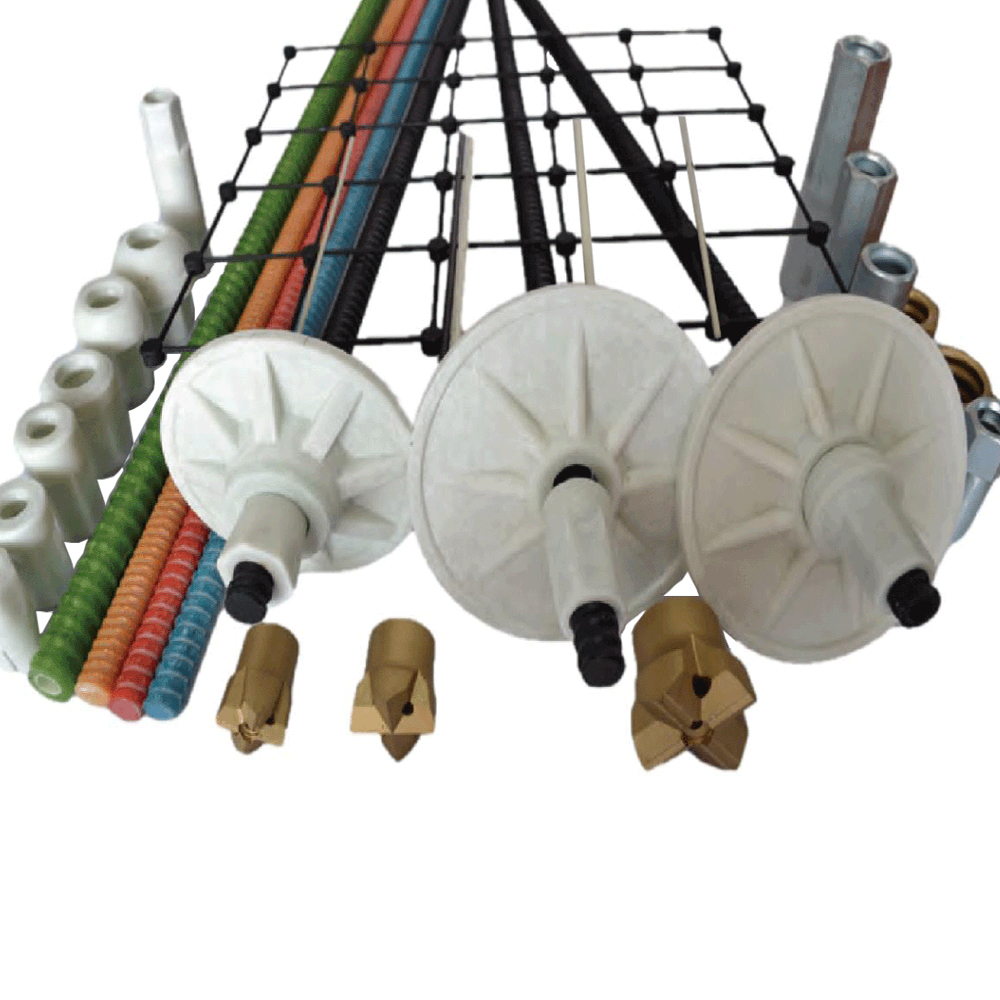
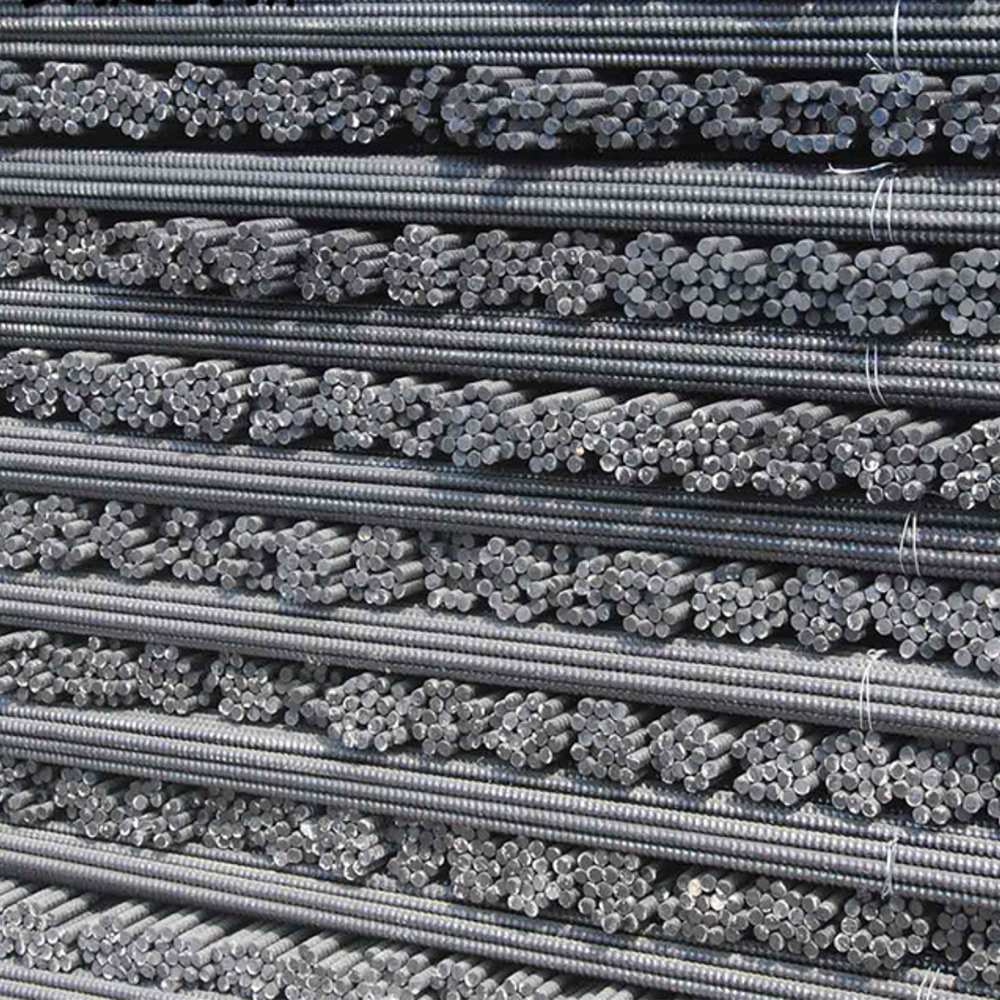
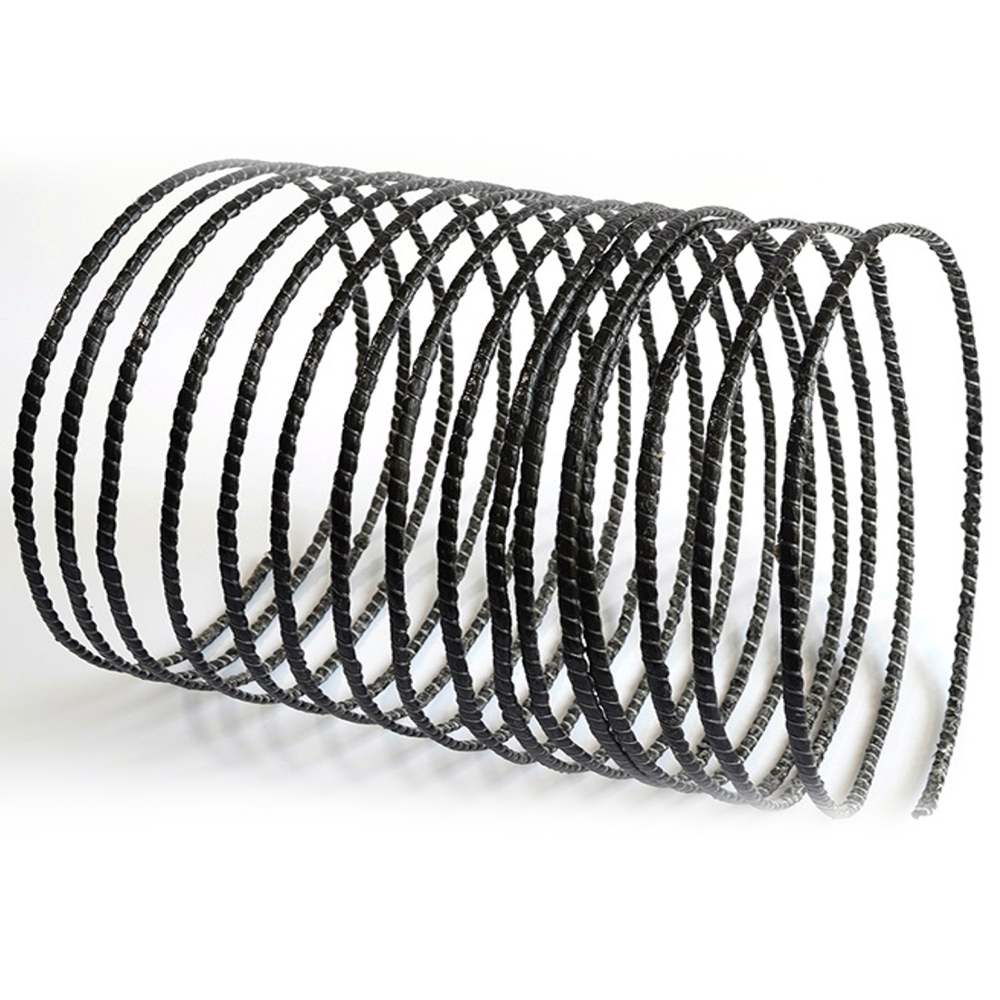
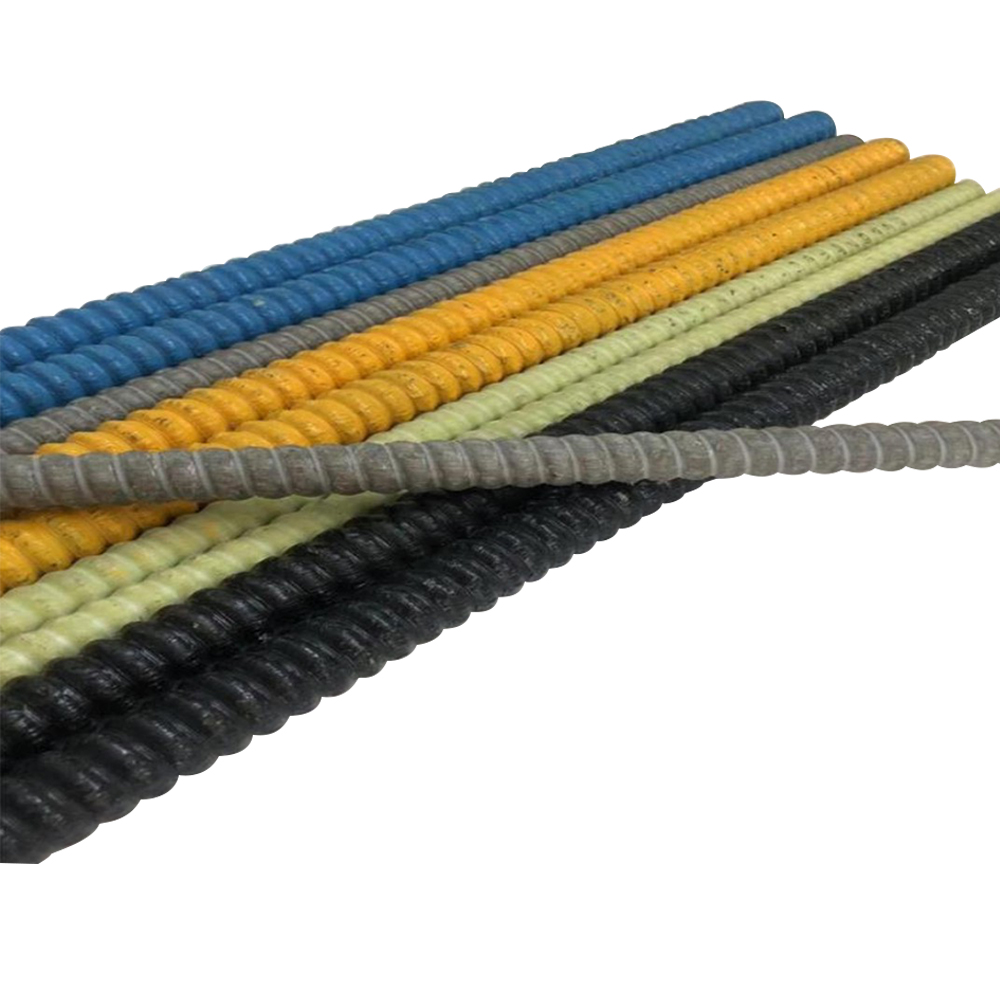
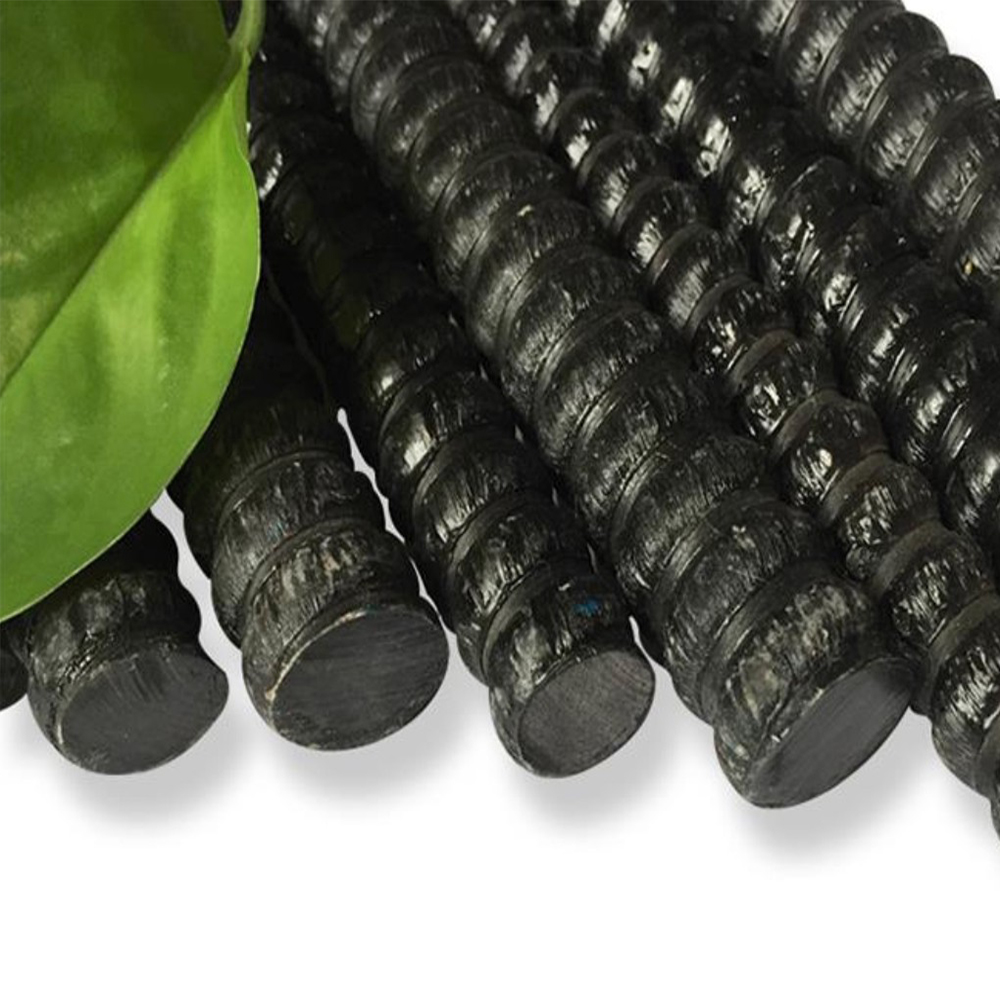
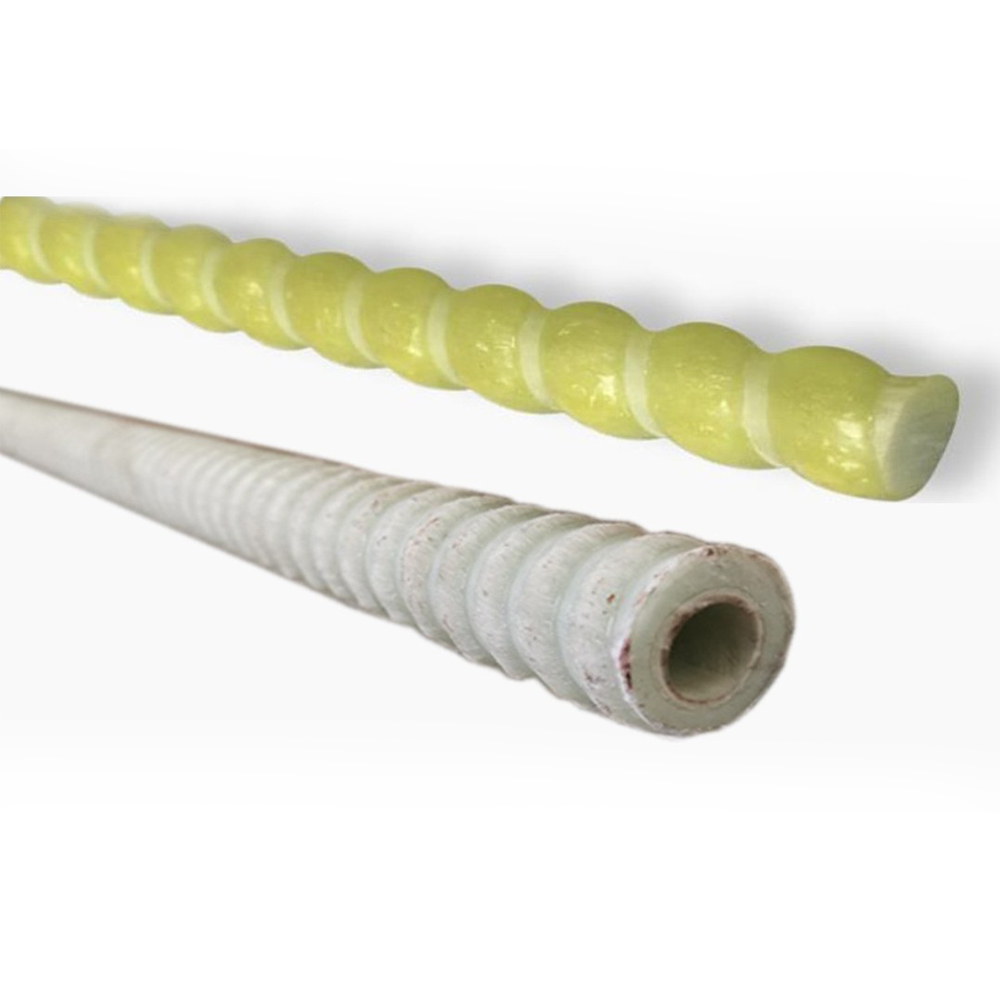
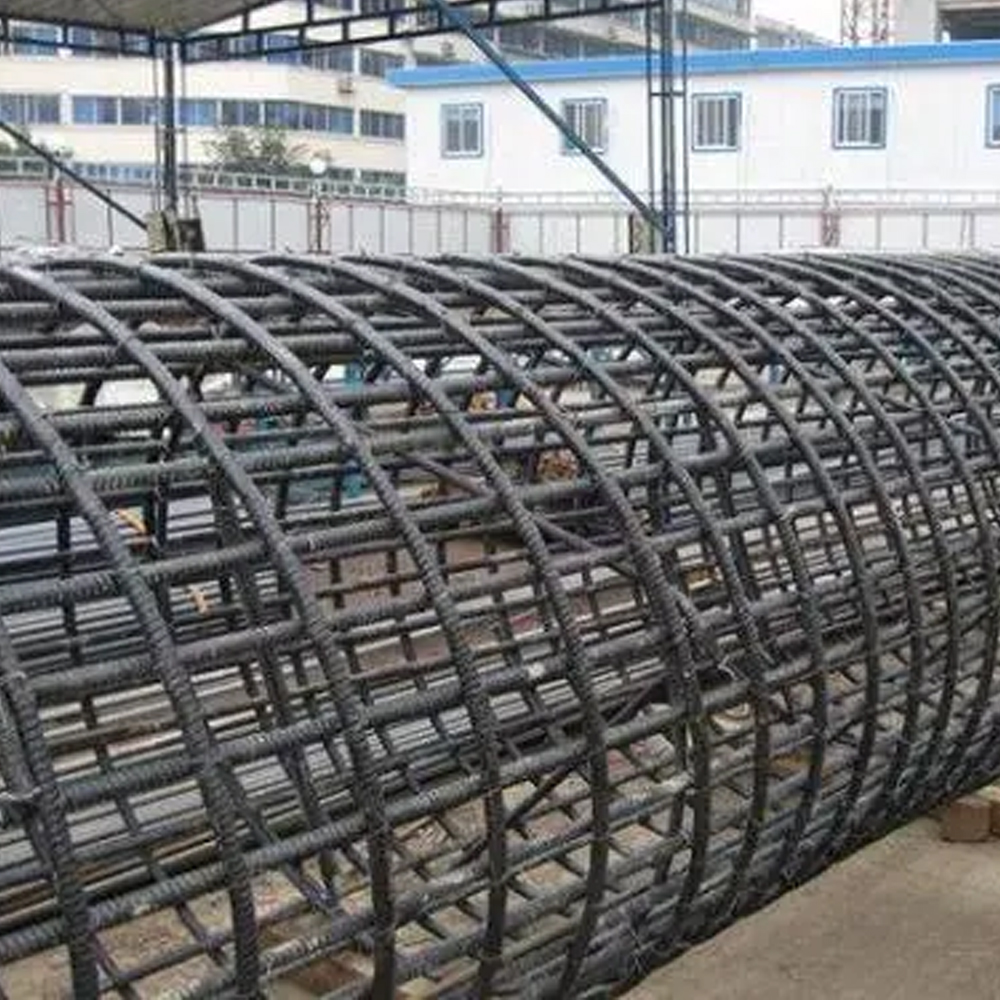
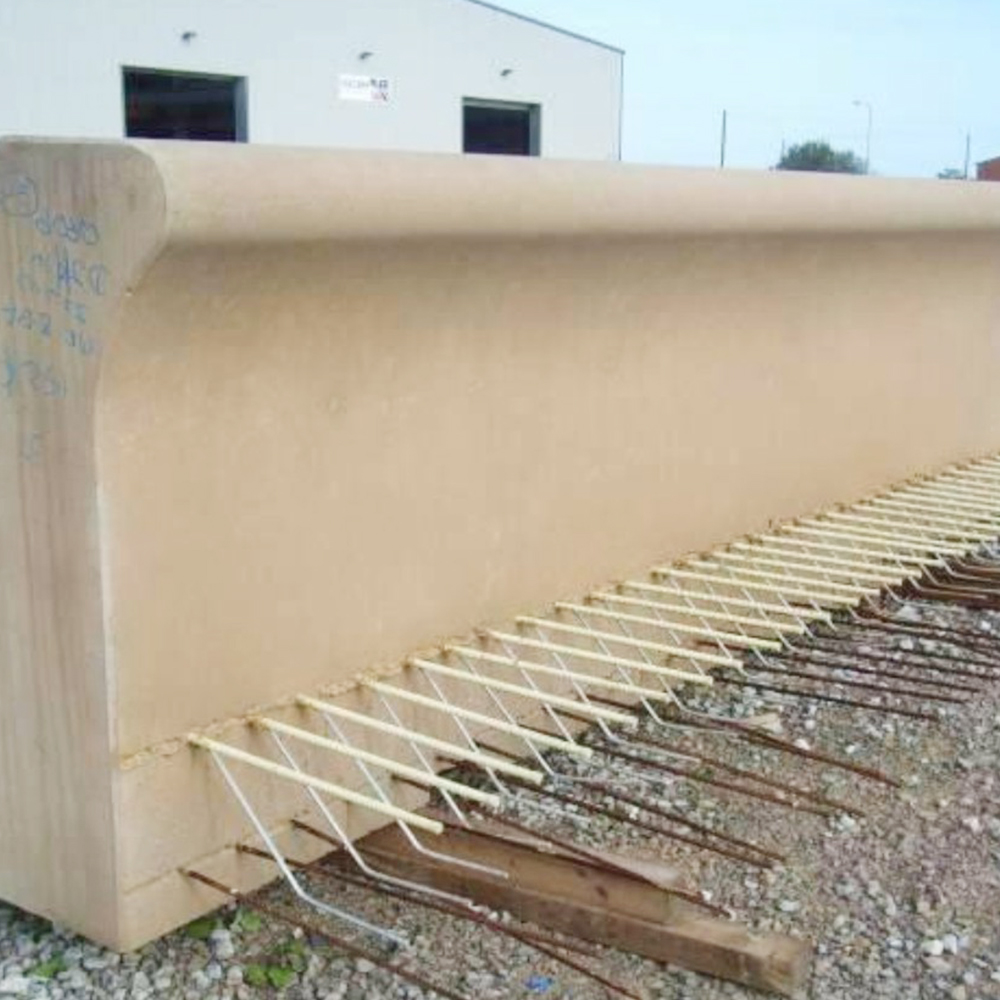
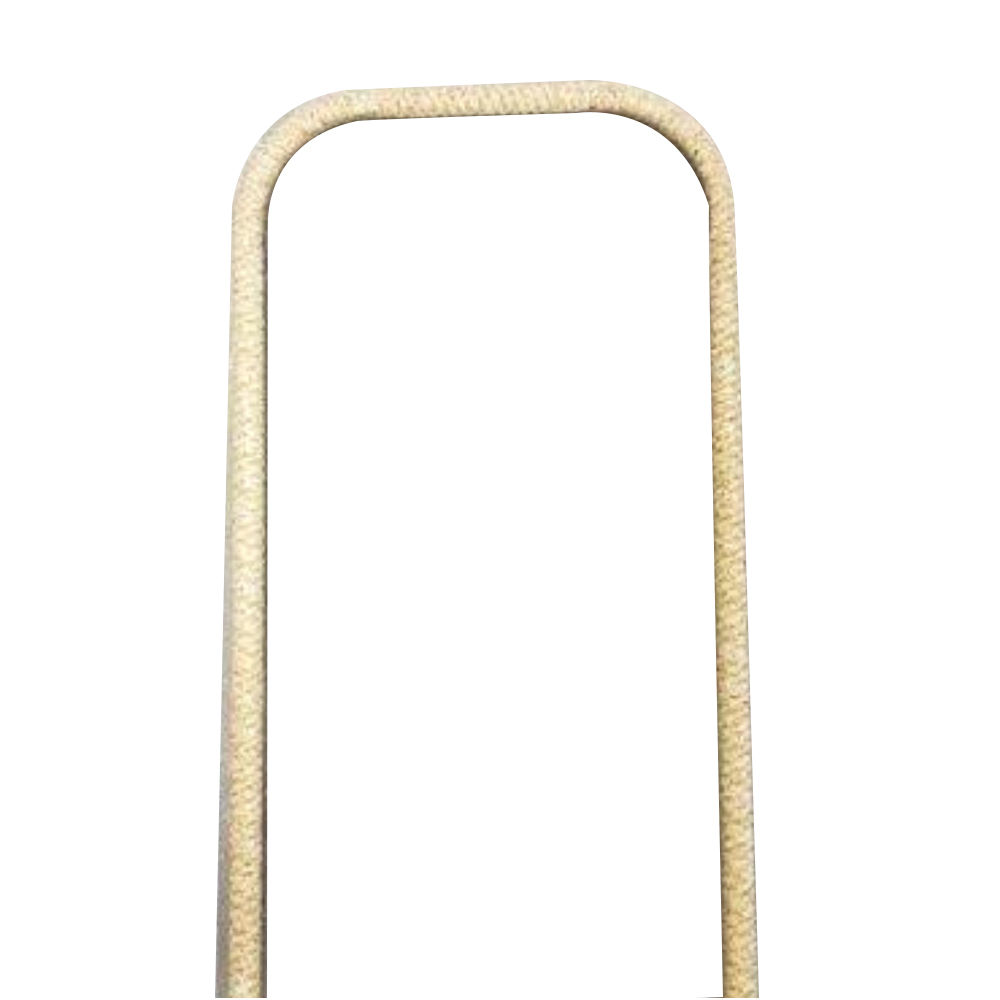
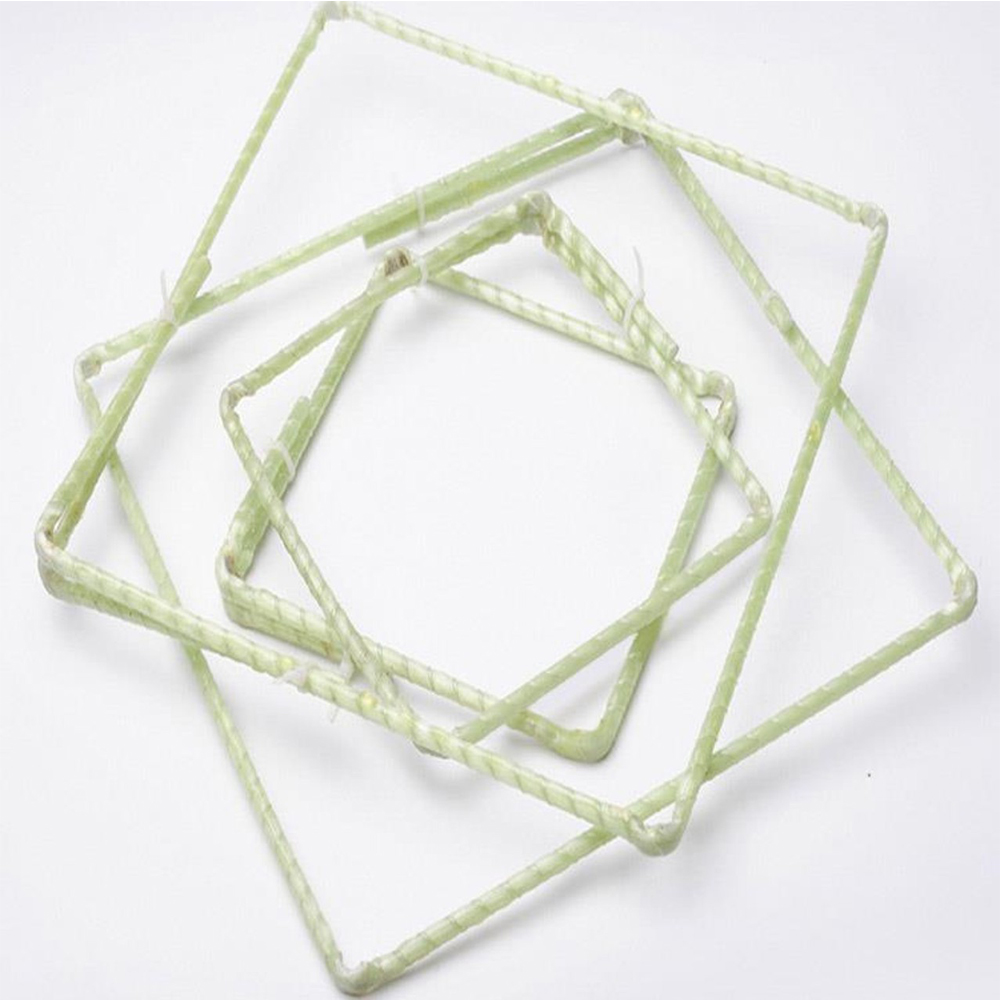
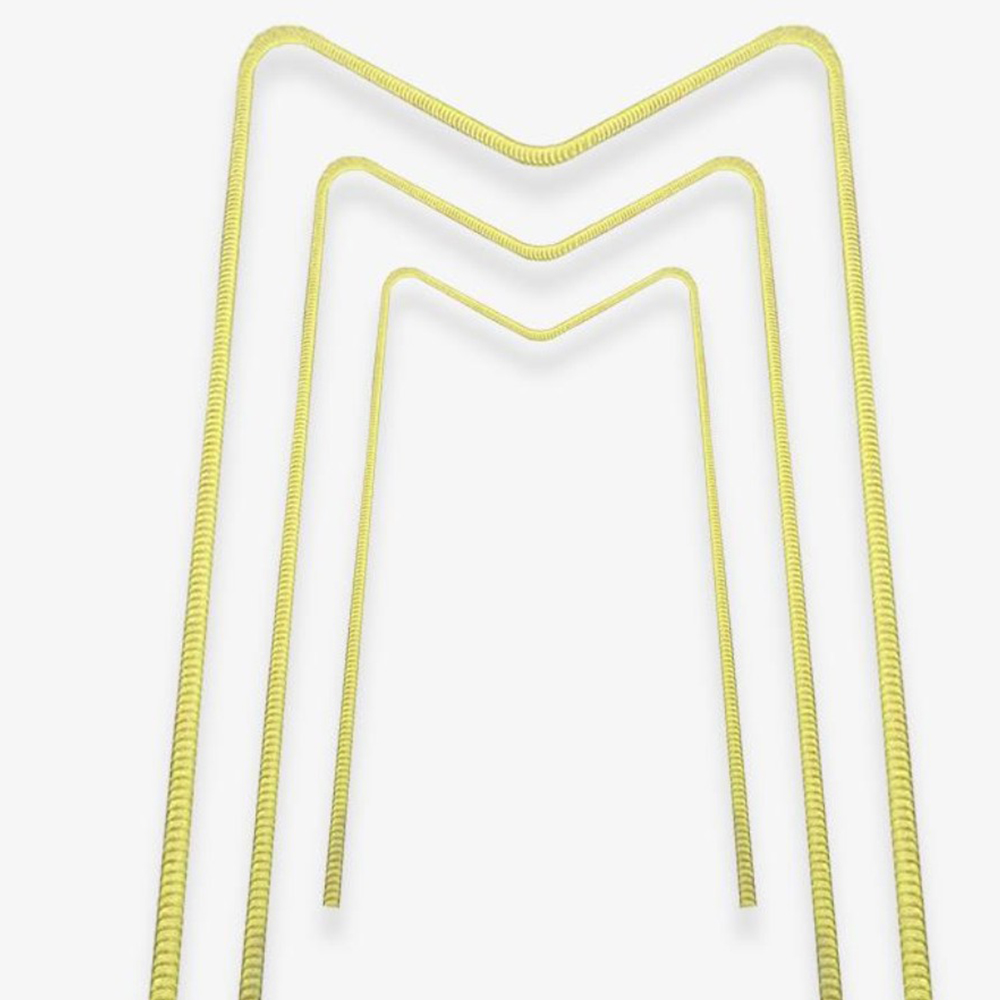
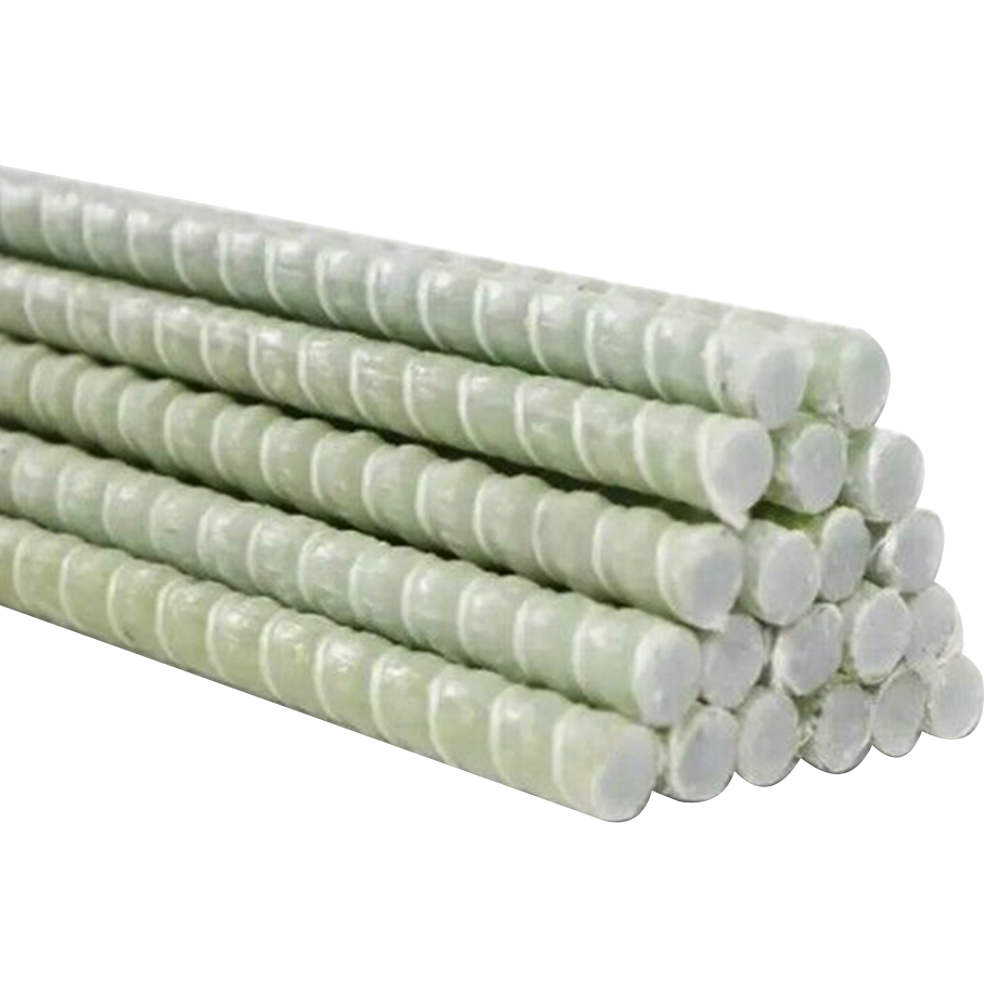
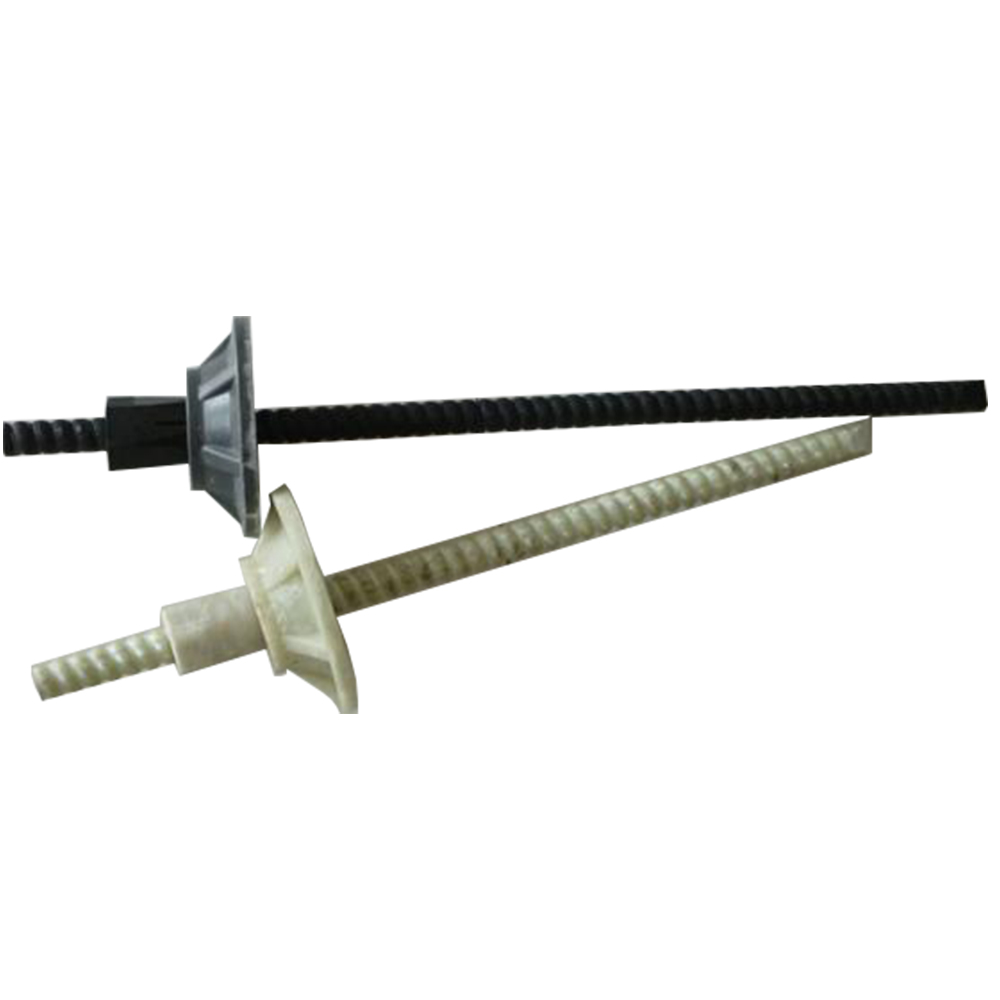
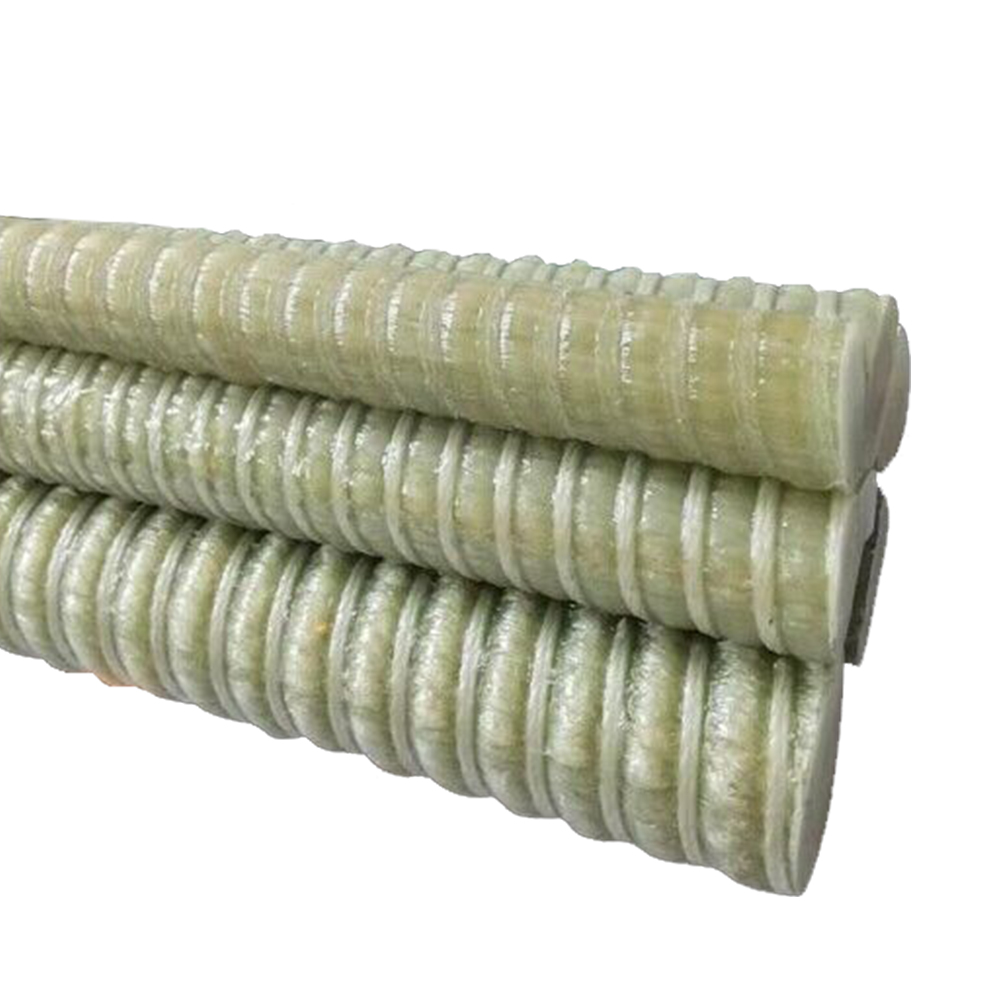
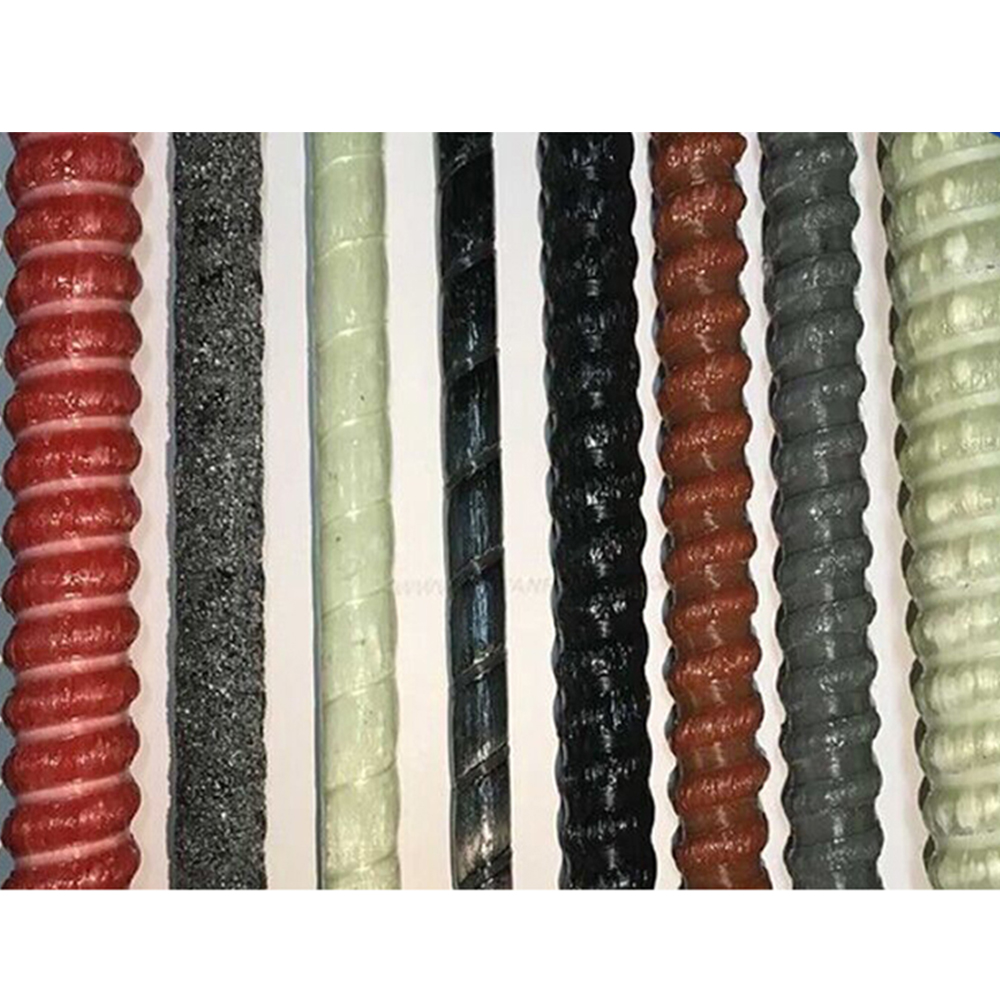
It is not proposed that basalt should replace steel in its entirety. Its application is for a specific use where there is a danger that normal steel bar may be compromised by close proximity of chemicals, acid and alkaline.
Most especially in maritime environments i.e. sea wall defences, transport infrastructure roads and bridges it will replace the necessity to utilise epoxy coated or galvanised rebar, neither options being absolutely fail safe, or stainless steel which is even more expensive than basalt rebar.
Basalt rebar is affording greater longevity in structures that incorporate it.
Main advantages:
- 2 times stronger than steel
- 5 times lighter than steel
- Basalt rebar is naturally resistant to alkali, rust and acids.
- Moisture penetration from concrete does not spall.
- Needs no special coating like glass fibre rods.
- Basalt rebar has the same thermal coefficient expansion as concrete.
- Smaller rods allow for more critical spacing and designs.
- Basalt rebar is easily cut to length with regular tools.
- Basalt rebar does not conduct electricity or induce fields when exposed to RF energy, great for MRI or data buildings.
- On average 60% less CO2 emission in final concrete structures due to production process, logistics and material optimization.
- Overall project cost is less than with steel rebar.
- Savings on logistics and installation.
Properties | Value |
---|---|
Diameter | 4-32 mm |
Length, up to | 12m (Ø to 8 mm –in coils 50-100 m) |
Tensile strength | 1,200-1,400 МPa |
Elasticity modulus | 50,000-55,000 МPa |
Density | 2 g/cm3 |
Heat conductivity factor | < 0.46 W/(m°С) |
Coefficient of extension | 2.5 % |
Electric conductivity | dielectric |
Corrosion and chemical resistance | very high |
Magnetic characteristic | non-magnetized |
Heat stability | up to 300°C |
Depending on the application, the mesh can have different density and cell size.
The construction mesh is made of basalt roving with acrylic impregnation and polyester thread. It is an effective and economically advantageous substitute to ta traditional steel mesh due to its strength, low thermal conductivity and long-term retention of its qualities in aggressive environment, loads and temperature changes. Basalt mesh can also be used in construction of industrial and civil buildings in seismic regions.
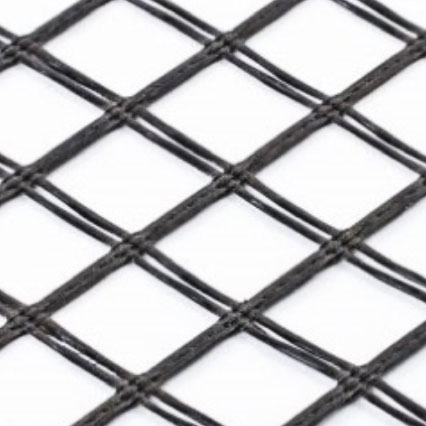
Basalt geogrid is designed for reinforcing road surface. It is successfully used in construction, repair and reconstruction of roads as a reinforcing layer. The main function of the material is uniform distribution of external load on the road over the entire surface, removal of internal stress of the asphalt-concrete coating, and also increase in the strength of the finishing layer of the asphalt to break.
Benefits:
- High strength and resistance to stretches and tears at high loads
- Ability to distribute the load evenly over the entire surface of the coating
- Resistance to deformation at high loads as a result of impacts
- Full ecological compatibility of the material
- Resistance to corrosive media, including chemical compounds
- Water-resistant in combination with excellent drainage qualities
- Fire safety and Fire Resistance
- Resistance to fungal spores and small rodents
- Ease of installation and dismantling
- Efficiency in the arrangement of road surfaces
- Resistance to seasonal temperature fluctuations and temperature changes during installation
- Long service life, reaching 35-40 years.
The geogrid has different areas of application. For example, it is possible to use the geogrid for both soil and asphalt concrete.
The basalt geogrid used for asphalt concrete strengthens the layers of construction materials, thus prolonging the operational period of the surface, and also stops appearance of cracks and gaps in joints.
Saving on building materials by using the geogrid reaches 35%. This is achieved by the special structure and properties of the materials used. And, importantly, the original structure of the construct remains which, moreover, becomes even stronger.
Weight per unit area, g/m2 | 250 | 500 | 750 | |
Breaking load, not less, kN / m | along | 50 | 100 | 150 |
across | 50 | 100 | 150 | |
Elongation at rupture no more than, % | along | 3 | 3 | 3 |
across | 3 | 3 | 3 | |
Admissible loss of tensile strength after 25 cycles of freezing – defrosting no more than, % | 5 | 5 | ||
Mass fraction of substances removed on ignition not less than, % | 18 | 18 | 18 | |
Dimensions of cells (±2%), mm | 25 | 40 | 40 | |
Roll width (±2%), cm | 540 | 540 | 540 |
Depending on the application, the mesh can have different density and cell size.
The construction mesh is made of basalt roving with acrylic impregnation and polyester thread. It is an effective and economically advantageous substitute to ta traditional steel mesh due to its strength, low thermal conductivity and long-term retention of its qualities in aggressive environment, loads and temperature changes. Basalt mesh can also be used in construction of industrial and civil buildings in seismic regions.
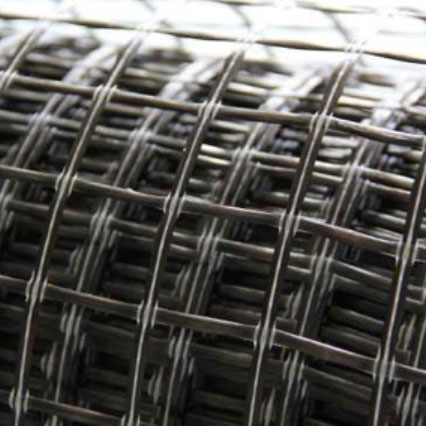
Benefits:
- High strength
- Low thermal conductivity, absence of “cold bridge”
- Light weight compared to steel mesh
- Resistant to corrosive environments and corrosion resistance
- Strength retention during the term of operation
- Compact and easy to use (cut with scissors and does not injure hands)
- Eco friendliness
Main application area :
- Reinforcement of horizontal masonry seams of bearing walls of various materials
- As bonds in a multi-layered masonry when joining layers
- Reinforcement of screeds
- Reinforcement of plaster wall layer of various masonry materials
- Increasing operational reliability of walls and partitions
- 30 % saving
General construction | Masonry | Blocks | Facade | ||
---|---|---|---|---|---|
Weight per unit area, g/m2 | 250 | 250 | 150 | 150 | |
Breaking load, not less, kN / m | along | 50 | 50 | 30 | 30 |
across | 50 | 50 | 30 | 30 | |
Elongation at rupture no more than, % | along | 4 | 4 | 4 | 4 |
across | 4 | 4 | 4 | 4 | |
Dimensions of cells (±2%), mm | 25×25 | 25×8 | 50×50 | 25×25 | |
Roll width (±2%), cm | 37-500 | 37-500 | 37-500 | 100-500 | |
Roll Length, m | 50 | 50 | 50 | 50 | |
100 | 100 | 100 | 100 |
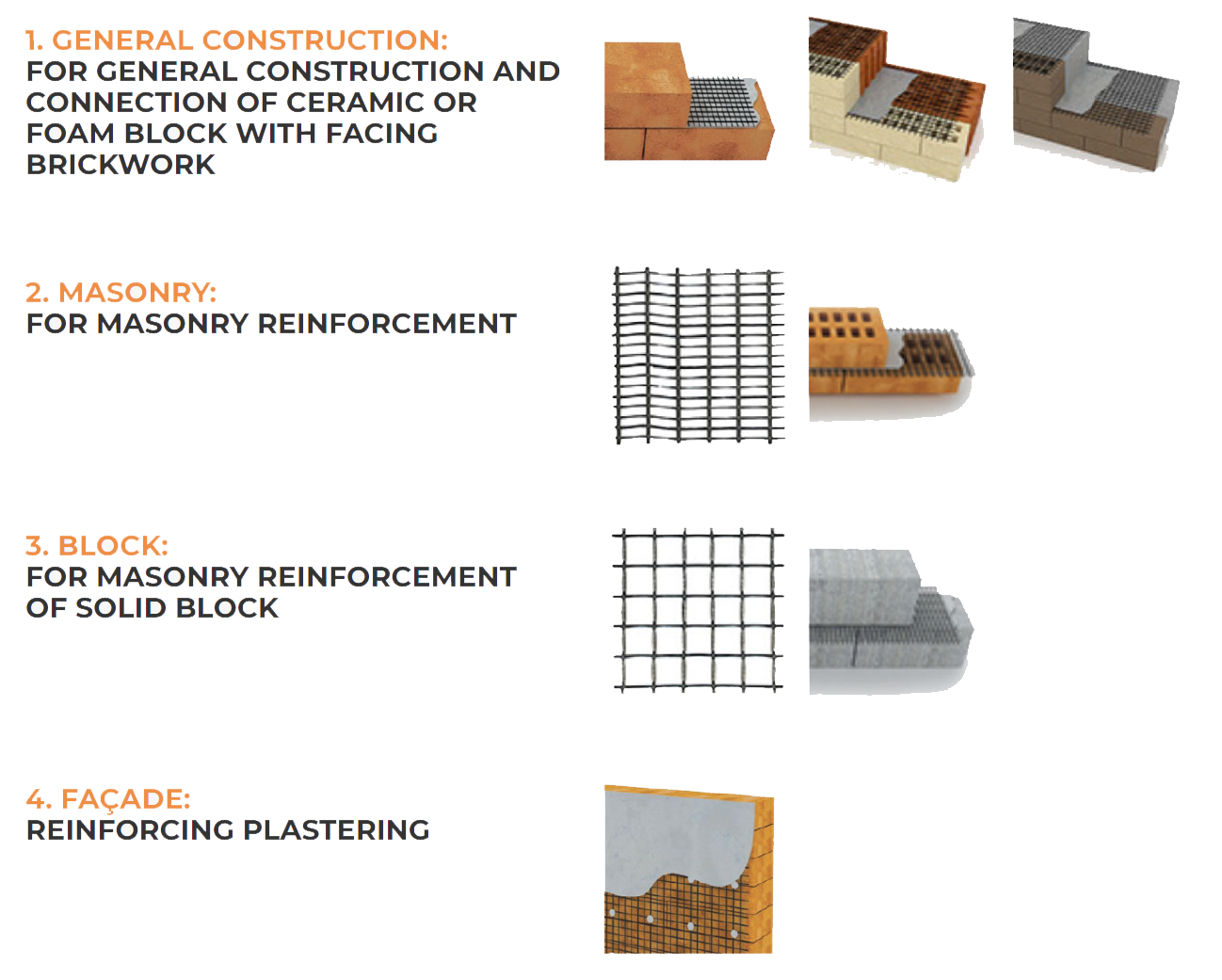
The main applications of basalt roving and basalt composites include mechanical engineering, aerospace, shipbuilding, automotive, chemical and oil industry, energy production, electronics, manufacture of composite building materials, public utilities.
Basalt roving is bundle of continuous unidirectional basalt filaments. It has high structural strength and resistance to aggressive environments. Basalt multi-end roving consists of mutifilaments produced at the continuous basalt fibre production facility and then assembled together in a doubling winder.
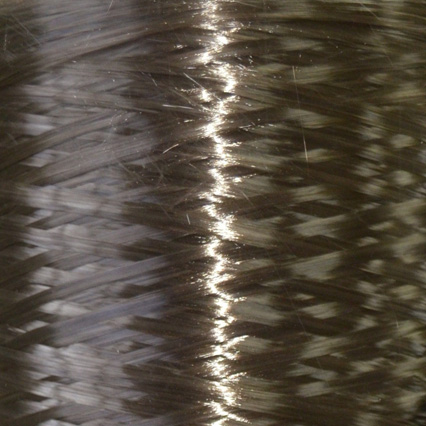
Benefits:
- High strength and low weight
- Very high alkali and acid resistance<
- Non-combustible and fire resistant
- Non-conductive and non-magnetic
- Radio transparent
- Does not absorb water
- Eco-friendly and safe, does not contain any carcinogens or toxic substances
Basalt roving | |
---|---|
Linear density, tex | 600 – 4800 |
ilament diameter, micron* | 9, 13, 17, 20 |
Filament diameter, micron* | 9, 13, 17, 20 |
Tensile strength (dry fiber), мН/tex | ≤ 650 |
Elongation at break, % | 3,5 |
Tensile strength in epoxy impregnated strand (ASTM D2343), МPa | 2900 – 3300 |
Tensile modulus in epoxy impregnated strand (ASTM D2343) GPa | 80 – 95 |
Temperature range, C | from -260 up to +700 |
Type of sizing – silane, sizing content < 1% | |
Bobbin type – external unwinding (with 75mm paper tube) or internal unwinding (tubeless) | |
Bobbin weight – upon request (not more than 10kg) | |
Standard packaging – 72 bobbins per pallet 120 х 80 cm |
* – roving with different filament diameter can be produced upon request.
Basalt fibre is a unique material for the manufacture of porous, foamed and aerated concretes, for adding into dry construction mixes to increase their plasticity, water-resistant and adhesive properties.
Basalt fibre is made by chopping continuous basalt fiblre into short lengths. Basalt fibre used as reinforcing agent for concrete, plaster and plastics, providing three-dimensional strengthening. To achiene better adhesion, uniform distributiona nd maximum reinforcing effect, depending on application area, it is necessary to selecta relevant monofilament diameter, cut length, moisture content, and sizing.
Basalt fibre | |
---|---|
Monofilament diameter, micron | fron 13 to 30 |
Cut length, mm | from 6 to 72 |
Temperature range, C | from -260 up to +700 |
Hydroscopisity, % | not mor than 0,2 |
Resistance to acids and alcalis | high |
Moisture content, % water | for concrete: 6-10 for production: 0,5 – 0,8 |
Sizing | Water compatible for concrete* Water incompatible for production |
Packaging | PE bags 10, 20, 25kg; jumbo bags 250 and 500 kg |
* fibre for concrete without sizing is available.
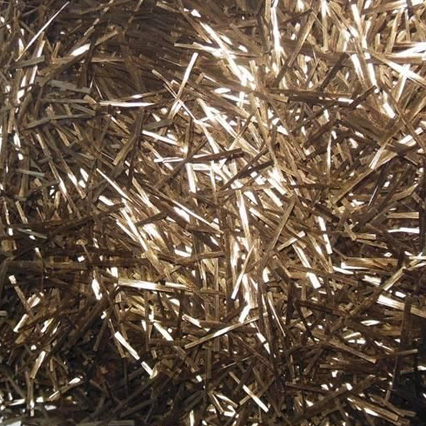
Basalt fibre reinforcement adds:
- crack resistance
- increasing durability of concrete
- tensile strength in bending
- frost resistance
- impact strength
- compression strength
- water resistance
Basalt fibre provides high adhesion to concrete ( «stone-stone») without deterioration of the reinforcing properties over time; it is a corrosion resistant material that does not get inflamed even exposed to open fire, it does not bunch up when added at any time of making and pouring the mix. Basalt fibre can be used for concretes with plasticizers and agents that change the setting time. Reduces cement and water consumption.
APPLICATION
Due to excellent durability, basalt fibre is highly suitable for reinforcing concrete used when strength requirements are especially high: floors, grounds, roads with heavy traffic of people or transport. High resistance to climatic factors and hygroscopic properties make basalt fibre essential for hydraulic structures and coast protection. Basalt fibre reinforced concrete finds its application in building earthquake-proof structures, explosion hazardous facilities, reservoirs and concrete pipes used for transporting aggressive substances and liquids with great number of abrasive particles, and nuclear and chemical facilities.
Basalt fibre is a unique material for the manufacture of porous, foamed and aerated concretes, for adding into dry construction mixes to increase their plasticity, water-resistant and adhesive properties.
Dry fibre with water incompatible sizing is used for the manufacture of brake pads and needle-punched mats.
Type of concrete structure, application | Quantity of fibre in mix | Length and diameter of fibre |
---|---|---|
Screed floor, industrial floors on a solid prepared base | 1% of cement weight (replacement of metal mesh) |
12 – 24 mm 16-17 μm |
Heavy loaded industrial floors on unprepared base | 1% of cement weight (in combination with rebar and mesh) |
12 – 24 mm 16-23 μm |
Intermediate slabs, columns, reinforced concrete frame | 1.5 kg per cubic meter | 12 – 24 mm 16-23 μm |
Buildings and structures foundations | 1.5 кг – 2 kg per cubic meter | 12 – 24 mm 16-23 μm |
Road construction, sites | 1% ( replacement of metal mesh) | 12 – 24 mm 16-23 μm |
Plastering solutions | 0.6 % | 6 mm 16 μm |
Cellular concrete products (foam blocks, gas blocks) | 0.25 – 0.4 % | 6- 12 mm 16 μm |
* fibre for concrete without sizing is available.
Working at the highest level
with our clients
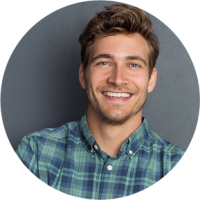
Karena Schuyler
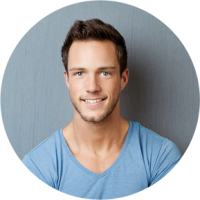
Roselee Breitenbach
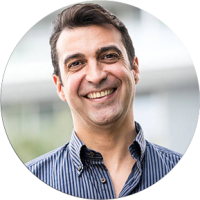
Johnson Salzberg
168/9, Bo Win, Si Racha District, Chon Buri, Thailand 20230
Phone: +66 (0) 96 408 0579
China Production Base
Add: No.9 Jingwei 10th Road, Jinghe Industrial Zone, Xi’an , China
Tel:+86-29-86031636 86031942 Fax:+86-29-86030621
China Line Hardware Base
Add: No. 158, Huafeng Road, Jintan District, Changzhou City
Phone : +86-18792660323
Canada office
Add: 190 Borough Drive, Toronto ON Canada, M1P 0B6
Tell:+1-647-728-1512